November 13, 2023
Reduce the risk of claims and disputes through deliberate, careful contracting and technical expertise
From the first industrial-scale, solar-driven green hydrogen facility in the Middle East and North Africa, to Oman's Sohar Titanium mining plant, to the United Arab Emirates' new Etihad national rail network, the Middle East is pushing forward with an ambitious slate of industrial facilities that will define the region's future, including Saudi Arabia's NEOM Green Hydrogen Company's carbon-free hydrogen plant, which promises to be the largest clean hydrogen operation in the world.
As owners, contractors, architects, engineers, and investors know, accomplishing groundbreaking feats in modern construction comes with a high probability of unforeseen technical engineering challenges, cost and schedule overruns, and almost inevitably, claims and disputes as a result of both. In Dubai alone, the Dubai International Finance Centre Arbitration Institute and the London Court of International Arbitration have reported year over year increases in the number and value of claims, and in 2022, the Dubai International Arbitration Centre handled 340 new cases, 49% of which involved construction disputes.
Commissioning as a key pitfall: how risk develops
Although claims can surface at any point during the construction project lifecycle, the commissioning process is an exceptionally high point of risk for complex industrial facilities with machinery and equipment involving thousands of components and interrelated operational elements.
Commissioning is not only the handover between contractor and owner when all pieces must come together seamlessly — it's the critical phase when any steps that were missed or overlooked throughout the build may be revealed, raising technical problems that lead to disputes.
There are many reasons why commissioning can go off track, several of which have to do with missed milestones earlier in the project lifecycle. For example, pre-component testing is sometimes rushed or skipped, as fixed price contracts can increase pressure on contractors to eliminate tasks to save costs and stay on schedule. In turn, a contractor might rely on prior testing such as component compliance testing or factory acceptance testing that doesn't translate to smooth installation and on-site integration.
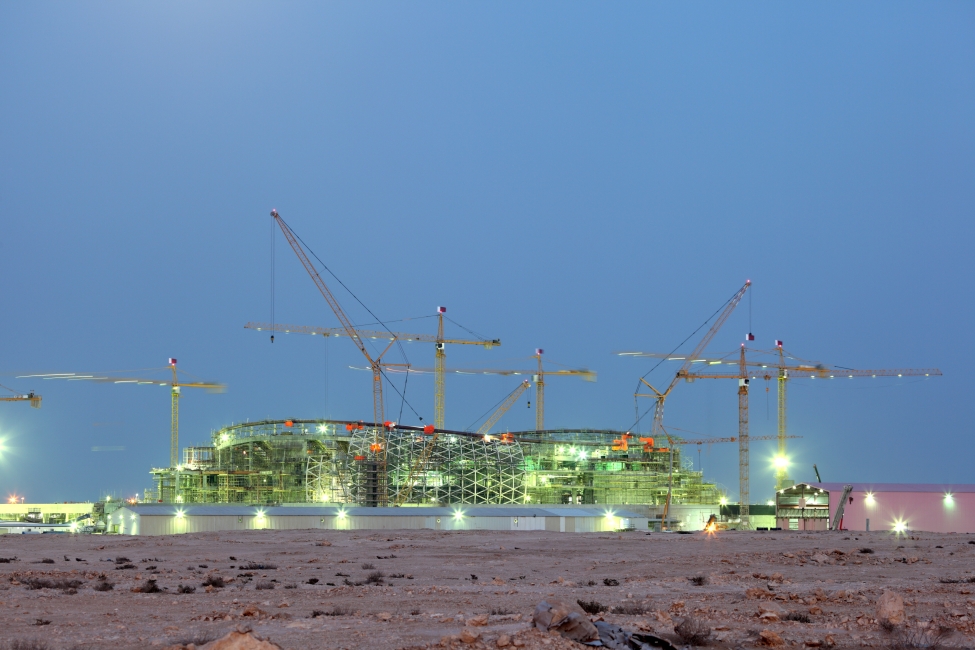
Ambiguous mid-project requirements can also challenge contractors and owners if testing targets aren't spelled out clearly. While requirements at the beginning and end of the construction project lifecycle are usually well defined, performance checkpoints in the middle are often less explicit. As a result, mid-project testing such as factory acceptance testing followed by site acceptance testing might be discounted as time consuming, redundant, or superfluous. However, skipping these steps can have severe consequences if commissioning fails due to faulty or inadequate components.
Significantly, when something does go wrong during the commissioning process, it can be incredibly difficult to deconstruct, much less absorb the need for design or component change. The visible or perceivable challenge may also only be the tip of the iceberg in terms of deeper, connected functions, resulting in the need to reverse engineer expensive, complex systems. In this scenario, multiple technical perspectives working together will likely be needed to completely understand the interplay between different elements, for example, electrical, mechanical, and structural components.
For all these reasons, by the time a project reaches commissioning, it's imperative that equipment and systems are already working together safely and effectively — and the commissioning process itself serves as a verification of two key questions (versus a live test of functional operations):
- System integration testing: Is the system completely functional and does the system meet operational requirements?
- Operational testing: Can the system meet its performance requirements under real-world conditions?
To help ensure both questions can be answered with confidence and reduce or limit the scope of claims, stakeholders need a strategy that supports commissioning from the very start of a project, first, through contractual specifications and, second, by laying the groundwork for operational success through mission-critical multidisciplinary technical expertise.
Whether or not a system "passes" a test often doesn't tell the whole story to stakeholders about the level of risk it could present in a broader functional context.
Contractual clarity: mitigating risk through clear requirements
Risks come in many shapes and forms over the lifecycle of mega construction projects. Engineering, procurement, and construction arrangements between contractors and owners are often driven by a singular goal for technical execution: delivering the project as required, on time and on budget. While some owners may perform extensive front-end engineering work to develop detailed project specifications, others leave the burden on the contractor.
Regardless of the arrangement, the facilities end up being commissioned. One way to ensure success at the end of the project is by making sure pre-commissioning testing is performed appropriately leading up to project delivery, something that should be detailed in the contractual agreements. This might include:
- Carefully thought-out, reasonable, and achievable preliminary schedules
- Realistic cost estimates
- Quality control milestones with clearly documented steps for testing protocols and system performance requirements
- Communication protocols for sharing the results of component and site-acceptance testing
In terms of communication, it may seem unnecessary to specify how the results of site acceptance or systems testing will be shared. However, whether or not a system "passes" a test often doesn't tell the whole story to stakeholders about the level of risk it could present in a broader functional context.
For example, an HVAC system that operates just below the required noise level during an acceptance test in winter months might operate at a much louder volume when working harder to cool buildings during the height of summer. As such, this would require implementing additional noise control measures to meet final performance requirements that could easily be missed. Embedding a process for communications at the contractual phase enables stakeholders to implement corrective measures much sooner — and more affordably — than later in the process, when they run a higher risk of resulting in delays, cost overruns, and associated claims.
It is often also worthwhile to consider building redundancies into the works when possible and cost-effective. If something does go wrong during mid-project testing, there's a strong likelihood that new or replacement specialty components and the labor needed to install them will not be readily available. Developing contingencies or alternatives can help avoid bottlenecks. Assuming quality control milestones are in place, both contractors and owners will be better positioned to direct inquiries to the right stakeholder; for instance, if factory acceptance testing was performed before the components arrived on site and didn't work as expected, technical experts may be able to quickly zero in on installation issues rather than potential non-conformities.
Technical expertise: ensuring complex systems come together safely
It's worth emphasizing that in addition to delivering a project, safety should be a driving factor of deliberate, careful pre-commissioning testing throughout the project lifecycle. Rushing through steps or building inadequate equipment that wasn't properly tested at the component level can put personnel and property at risk of damage if a failure occurs.
To prevent costly delays, finding and fixing the root cause of complex failures in complex systems is essential. The range of large, high-profile facilities planned throughout the Middle East, where the operating environment includes high heat, sand/dust, humidity, etc., presents unique challenges. The nature of these industrial facilities will also require a variety of technical disciplines and types of expertise.
Equally, when something goes wrong, it's logical that whatever appears to be the challenge on the surface — say, a mechanical failure — will result in the first expert to arrive on the scene — a mechanical engineer. However, overlooking the inherent requirement of interrelated systems and the involvement of multidisciplinary technical experts can result in significant delays and additional costs if the appearance of the first problem belies more trouble underneath. Stakeholders can find themselves working piecemeal trying to get to the bottom of a challenge, bringing in one technical expert after another and re-explaining the situation each time — with the risk of information gaps growing.
Building the mega facilities and infrastructure that will define the smart cities of the Middle East reflects an interesting mix of advantages and challenges.
Failures of individual components in the types of large, complex systems involved in mega construction projects also often mask or prevent the discovery of more complex system failures, meaning resolving the surface problem may cause breakdowns to surface elsewhere. Or the initial problem may look like multiple points of failure that share a single underlying cause. In either scenario, the ability to tap into multiple perspectives and rely on experts who can work fluidly together offers the best chance of minimizing disruptions to broader timelines and costs.
The perspective of siloed experts may also preclude an effective solution that requires collaboration and communication. If a problem is occurring with a system's electrical wiring, what does the proposed fix imply for nearby piping and ducts? If a monitoring system is broken, what could that mean for the mechanical systems relying on those trends? If a pipeline is cracked, how does it affect a pump downstream from the failure? Or, if a compressor is vibrating excessively, what impacts might be expected to the surrounding equipment?
Bringing best-in-class facilities to best-in-class cities
Building the mega facilities and infrastructure that will define the smart cities of the Middle East reflects an interesting mix of advantages and challenges. On one hand, existing development in future-focused cities like Neom, Abu Dhabi, Doha, Dubai, Riyadh, and others shows the power and vision of the region to bring together advanced technologies, materials, equipment, and workmanship. On the other hand, bringing complex, leading-edge industrial mega facilities online poses steep technical challenges — in addition to the operational demands of the Arabian Desert.
Commissioning is integral to ensuring that a facility functions and produces as intended at scale — and should be viewed as a final verification and documentation of work well done rather than a live testing phase. With an eye toward taking every possible step to avoid claims and disputes that can threaten the overall goal of a project, bridging the distance between the region's ambitious vision and ambitious facilities can be best supported by undertaking a careful, thoughtful, quality-focused contracting process and ensuring the right diversity of technical expertise.
What Can We Help You Solve?
Exponent's multidisciplinary experts are uniquely positioned to provide our construction and infrastructure clients with a variety of quantum and delay and engineering services. We offer independent, objective advisory support for all facets of claims and disputes, as well as technical analysis and expert testimony for alternative dispute resolution and international arbitration processes.
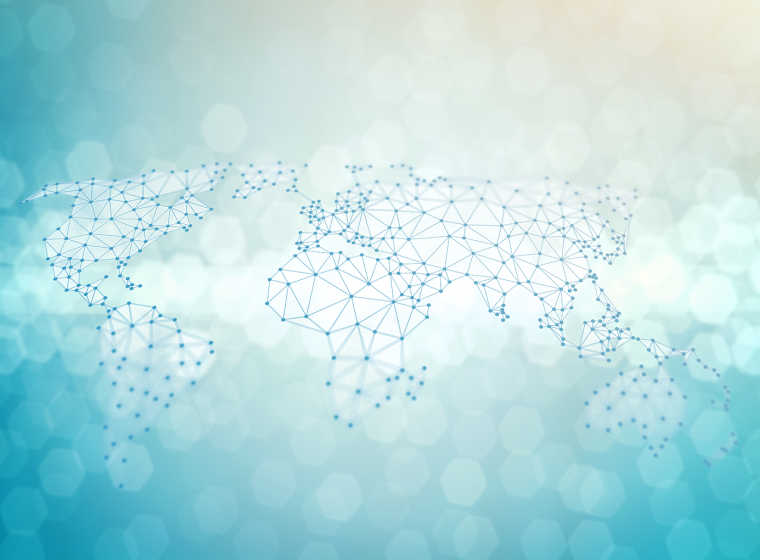
International Arbitration
For over 50 years, Exponent has provided independent expert advice to clients involved in arbitration and mediation all over the world. Our experience in courts...
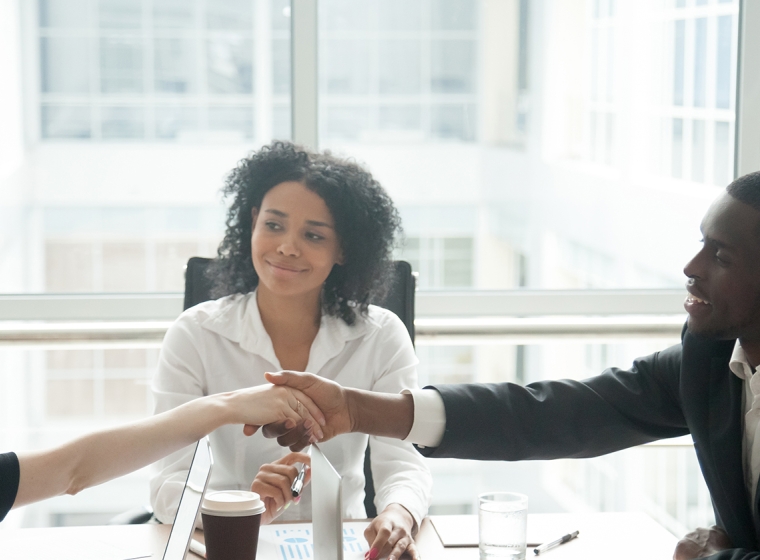
International Arbitration for Construction Challenges
Extensive international arbitration support for construction challenges and disputes.
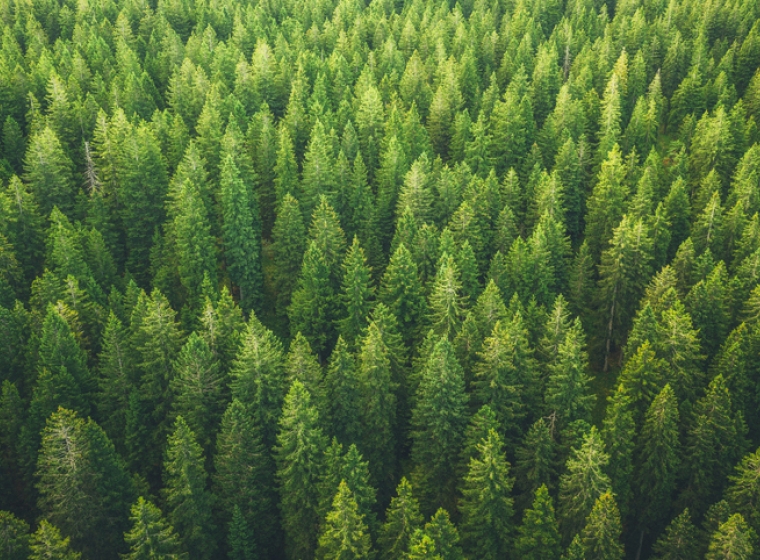
Environmental Consulting for International Arbitration
Objective, evidence-based insights for claimants, respondents, or arbitration panels.
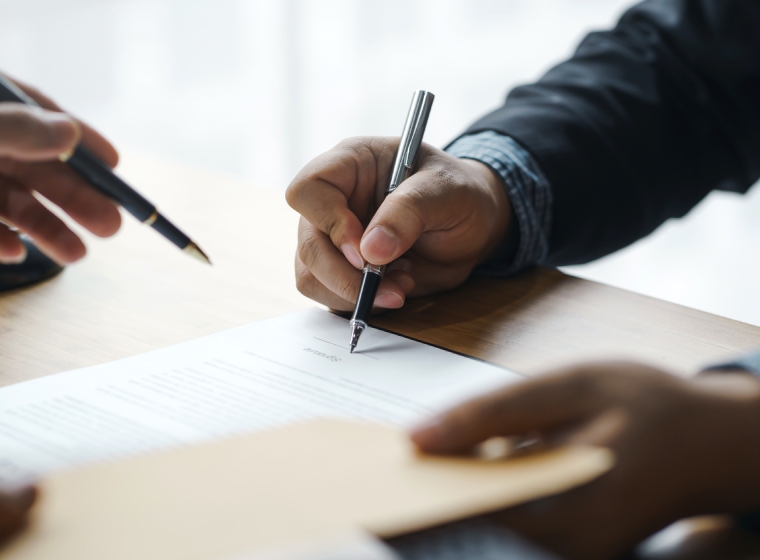
International Arbitration & Materials
Full lifecycle support for issues of international arbitration regarding materials.
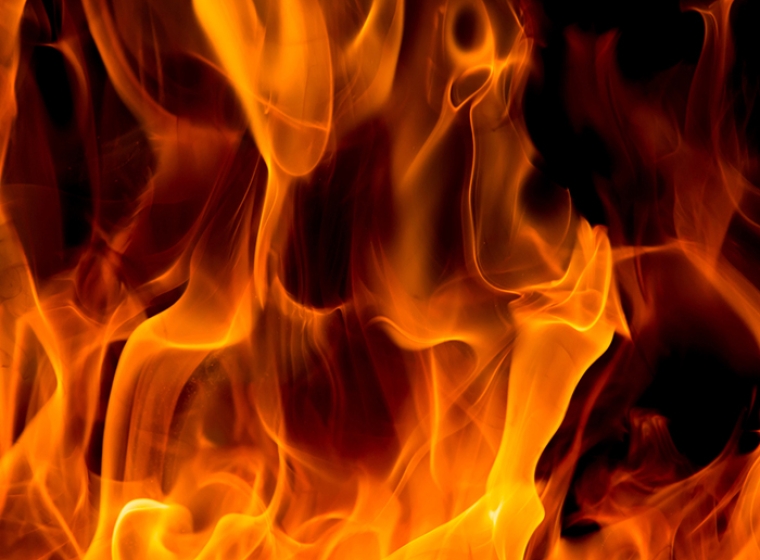
Thermal Sciences
Uncover root causes of fires, explosions, thermal, and flow-related accidents across industries.
Insights
Vessel Bridge Impacts: A Structural Engineering Perspective
Do You Know Where Your Aldyl A Pipe Is?
Sounding Out Community Noise Complaints
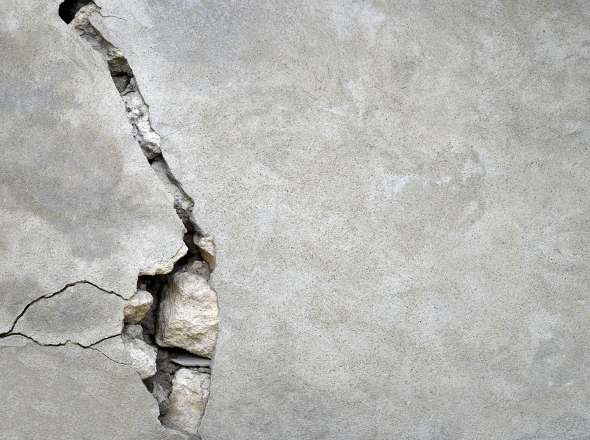