How do you optimize the reliability of your discreet components and printed circuit boards?
Printed circuit boards — the boards that carry discrete components and route circuits — are often the root cause of analog and digital device failures. Our PCB and discrete component projects typically involve failure analysis, design reviews, and electrical simulation of the components in a circuit. Exponent's electrical engineering and computer science professionals examine PCBs using both scanning electron microscopy and energy dispersive spectroscopy techniques, which assist in identifying potential liquid ingress or corrosion, while techniques such as infrared imaging and mechanical cross-sectioning — combined with high-resolution metallography — are used when analyzing PCB damage or failure.
Issues like metallic whiskers, conductive filaments, and dendrites are other frequent causes of electronic device or material failure. In these instances, our experts across multiple disciplines often work together to identify and address issues in PCBs that range from manufacturing to end-use.
For quality, risk, and reliability analysis, our engineers perform stress testing as well as replication testing to determine the specific root cause of a failed component or device. Our failure analysis begins with component-level inspection of the device. Deeper analysis may involve cross-sectioning by mechanical polishing or use of a focused ion beam to examine the structure of a component or PCB at a micron scale or below. Engineers in Exponent's Materials and Corrosion practice are frequently consulted when electrical failure is believed to have stemmed from a component material failure.
services
For 50+ years, we’ve thrived on solving unstructured problems that require bespoke solutions. Some of our services include:
• Structural and material analysis (using SEM/EDS)
• X-ray or CT imaging
• DC and AC resistance measurements
• 4-point resistance measurements
• Capacitance and inductance measurements
• Current-voltage (I-V) curve characterization
• Frequency response
• Infrared thermal imaging
• Semiconductor hot-spot measurement using emission microscopy or infrared microscopy
• Stress and replication testing
Our Capabilities Are Unparalleled
With expertise in over 90 disciplines and hundreds of capabilities, tools, and methodologies — we get to the root of even the most complex challenges and give you the objective answers you need.
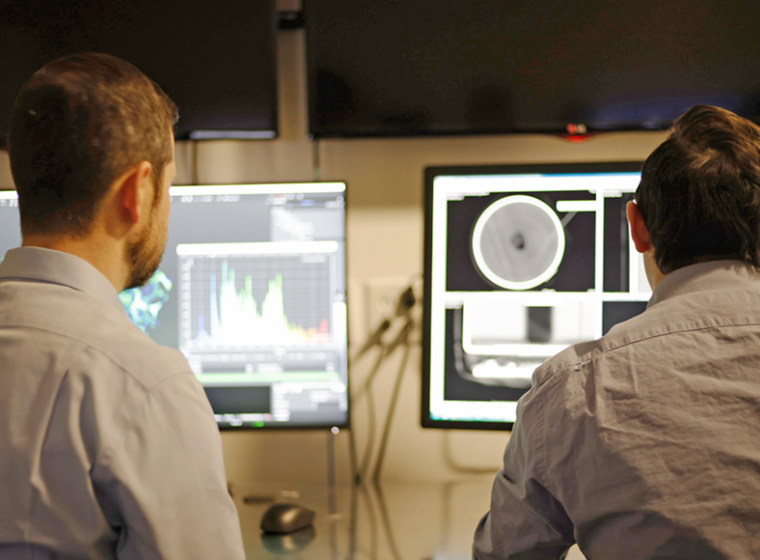
Software & Computer Systems Support
Insights and solutions for the design, development, and analysis of software prototypes, products, and platforms.
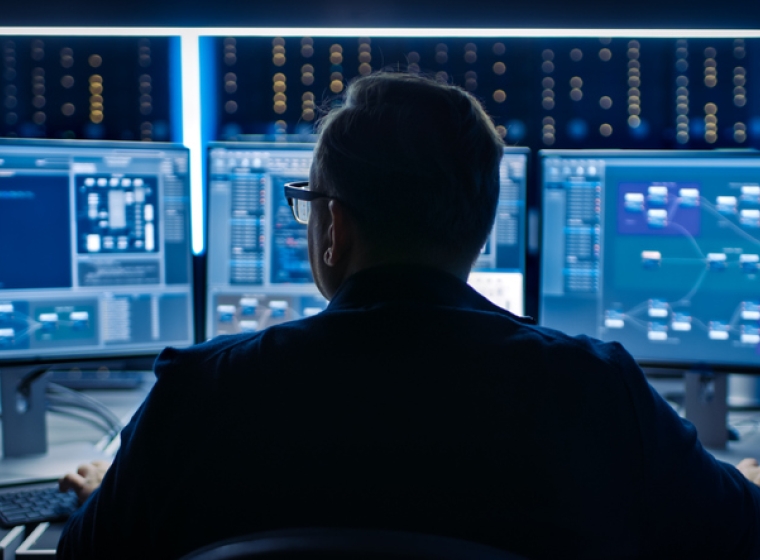
Systems & Controls
Critical systems and controls support, from missile guidance and ADAS technology to utility power generation and consumer electronics.
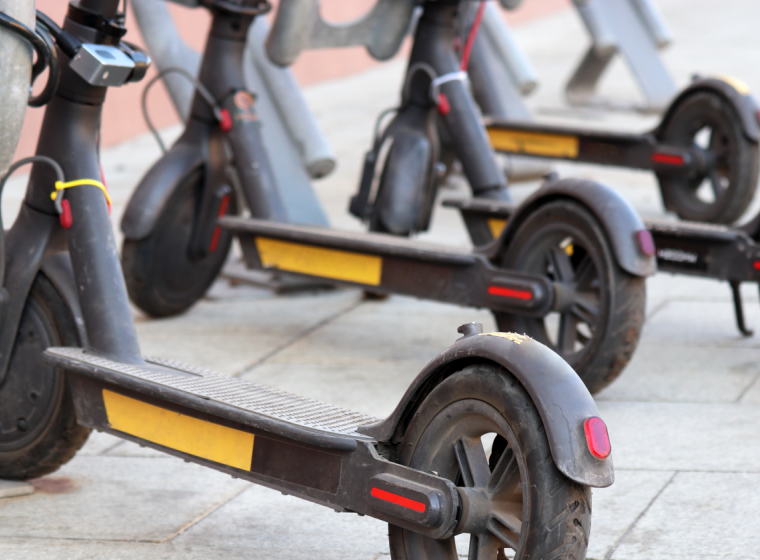
Electrical Devices & Consumer Products
Product design validation, risk assessment, product launch support, failure analysis, product recalls, and more.
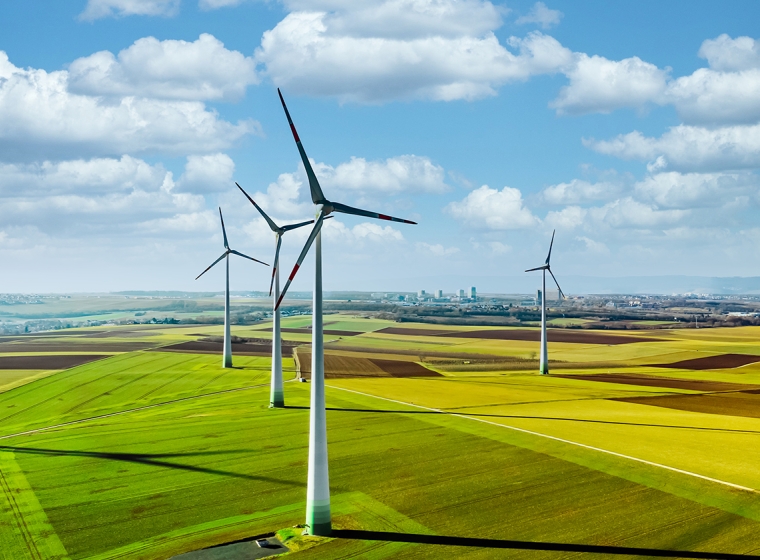
Power & Energy
Multidisciplinary support for high-power energy systems of all sizes in a variety of applications.
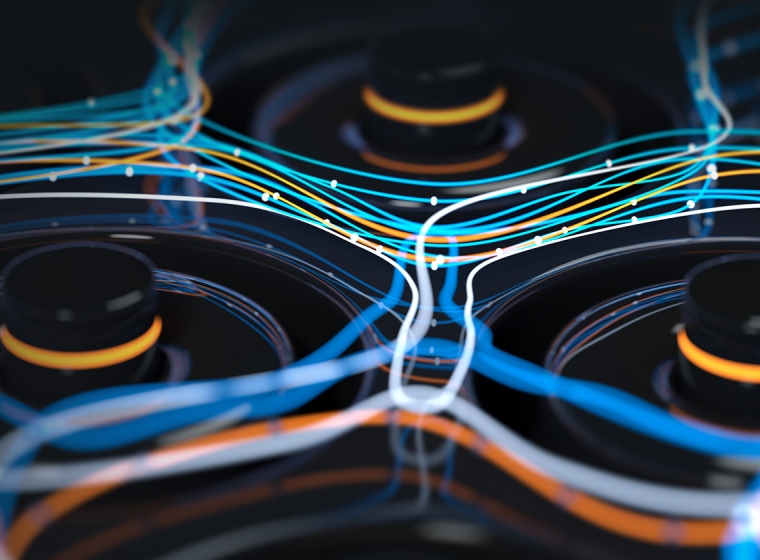
Batteries & Energy Storage
Supercharge performance, reliability, and safety across all stages of the battery and energy storage product lifecycle.
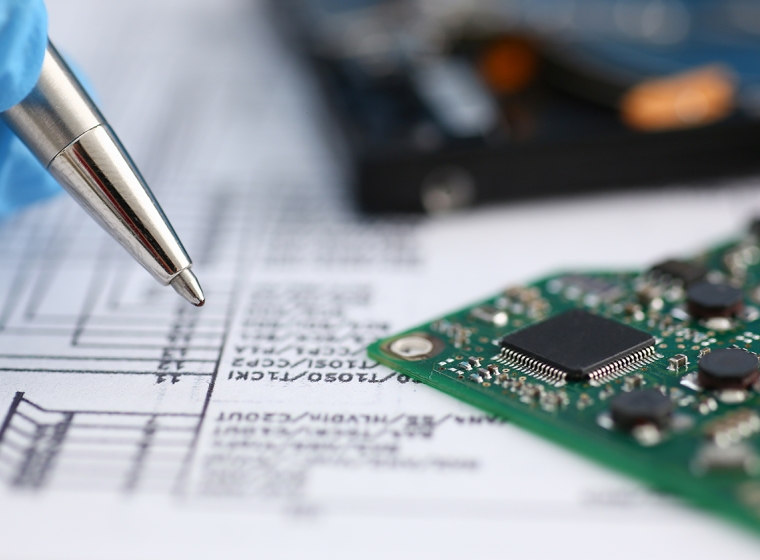
Electrical Engineering & Computer Science Expertise for Intellectual Property
Leverage best-in-class electrical engineering and computer science consulting for IP challenges
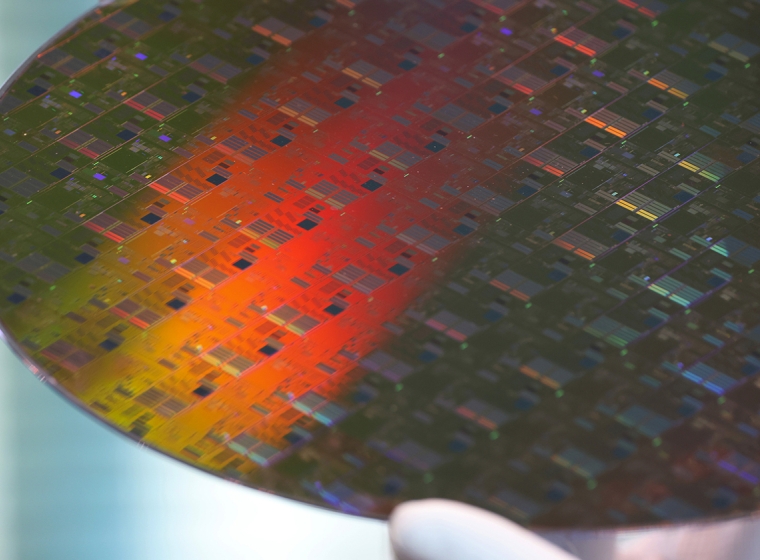
Product Development
Expert electrical engineering and computer science consulting services for every stage of your product journey.
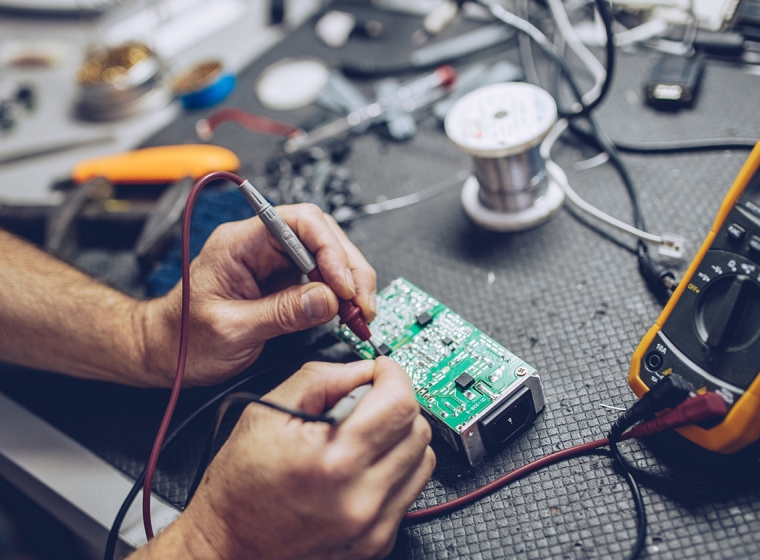
Technical Forensics
Failure analyses, predictive modeling, and accident reconstruction for valuable insights that help you prevent accidents and failures.
Experts
Our global and comprehensive expertise across industries gives us a deep understanding of current challenges, best industry practices, and the implications of emerging technologies.
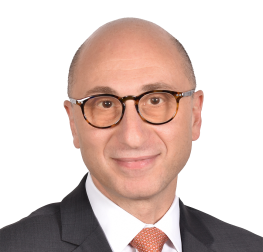
Corporate Vice President, Practice/Office Director and Principal
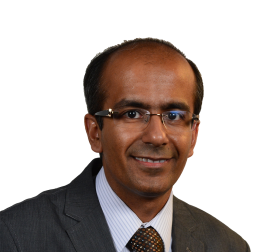




Senior Managing Scientist
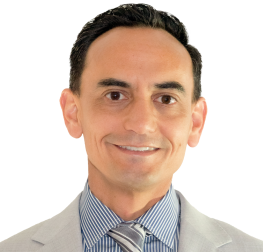
Senior Managing Engineer
