How does Exponent's multidisciplinary approach provide better process evaluations and quality control audits?
When clients face issues with their final products or if manufacturing machinery goes offline, clients turn to Exponent for rapid response and a value-driven approach. Our electrical engineers, computer scientists, data scientists, mechanical engineers, and manufacturing experts work to determine root causes of failures, assess process control and quality control, and evaluate supply chains — examining every angle for accurate understanding.
How can our value-driven, process-oriented focus help you improve performance and product quality?
With more than 50 years in failure analysis, Exponent's auditing programs are designed to help you improve the performance of the process and quality of your product while minimizing the risk of failures.
Our engineers have a strong background in ISO 9001 auditing techniques and principles and will help you develop best practices. But what enables Exponent to provide unparalleled value is our knowledge of how products fail in the field and how the manufacturing process can contribute to such failures. Our audits have a process-oriented focus — where the root of most manufacturing problems occurs — and target the quality systems associated with the process.
Gain peace of mind with our on-site investigations and factory audits.
Exponent conducts engineering audits of manufacturing facilities to help ensure suppliers follow best practices in manufacturing processes and quality control. In addition to full factory audits, which include an evaluation of the entire manufacturing process from incoming material quality control (IQC) to outgoing quality control (OQC), Exponent frequently visits manufacturing lines as part of our root-cause analysis investigations.
By examining various manufacturing and handling processes, we can assess whether contamination, mechanical defects, tolerance errors, and physical and chemical control parameter settings could have contributed to failures.
We have experience working with many different types of products, including but not limited to:
Battery cell (a range of chemistries)
Battery pack assembly
Connectors
Capacitors
Inductors
Resistors
Varistors
Flip chips
Clean room evaluation
Semiconductor fabs
PCB/PCBA
Ambient light sensor plating
LED and LCD displays
Adhesive application and curing
Metal forming
Metal casting
Polishing/grinding/finishing
Surface treatment
Anodization
System assembly
Injection molding
Capabilities & Services
Our Capabilities Are Unparalleled
With expertise in over 90 disciplines and hundreds of capabilities, tools, and methodologies — we get to the root of even the most complex challenges and give you the objective answers you need.
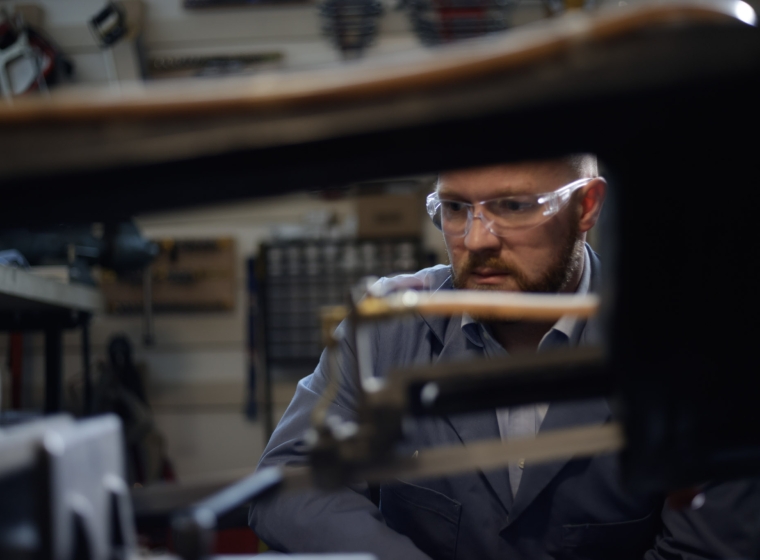
Mechanical Engineering Specialties
Mechanical engineering support to help solve complex problems within commercial and industrial applications.
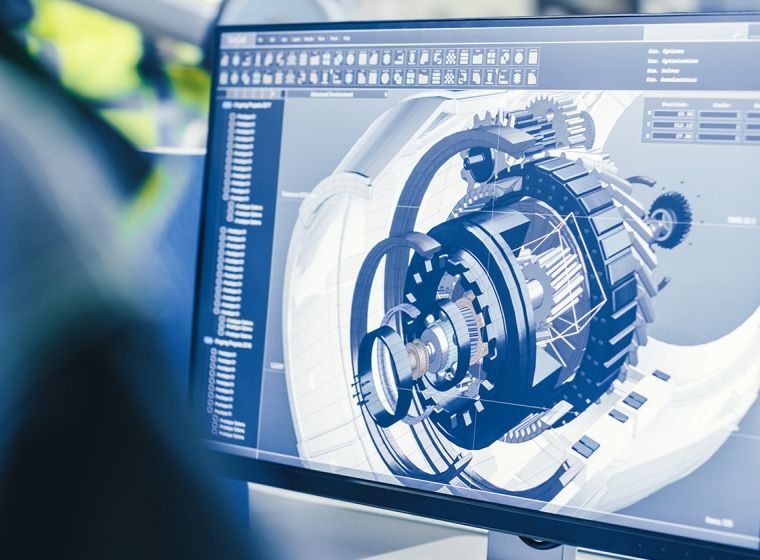
Mechanical Design Support
Mechanical design and testing support services, including customized mechanical modeling, finite element simulations, and system-level testing.
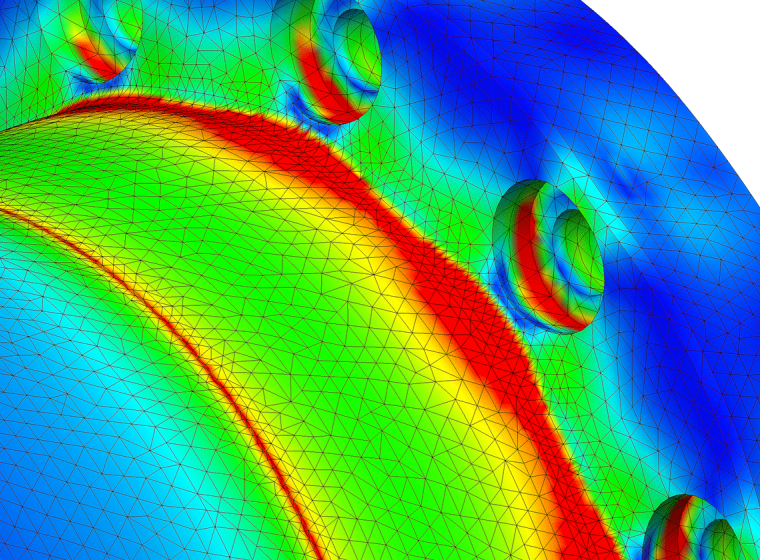
Mechanical Failure Analysis
Discover the root cause of mechanical failure using visual modeling simulation, data analysis, on-site investigations, and laboratory testing.
![Factory Auditing & Assembly Line Evaluations [ME]](/sites/default/files/styles/cards_home_card/public/media/images/GettyImages-1320492982.jpg?itok=To40IGtt)
Factory Auditing & Assembly Line Evaluation
Understand highly integrated automated machinery challenges and mechanical problems across diverse industries.
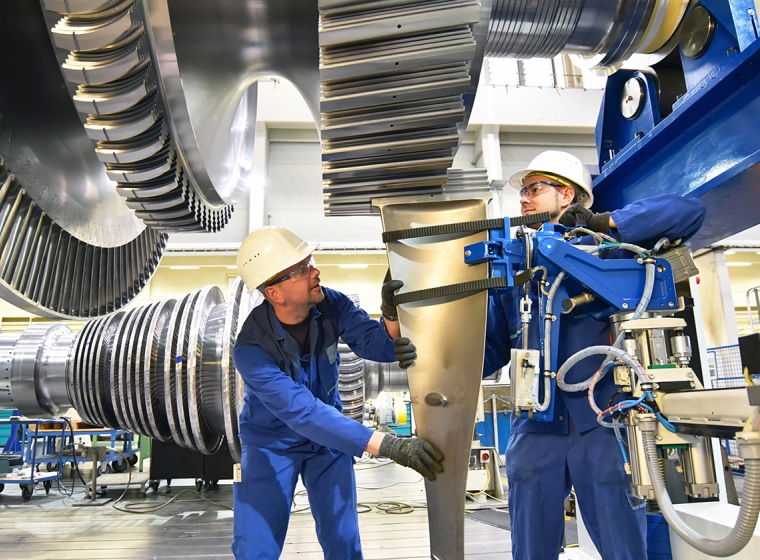
Risk & Safety Analysis for Mechanical Engineering
Multidisciplinary risk assessments, equipment safety evaluations, and occupational safety analysis.
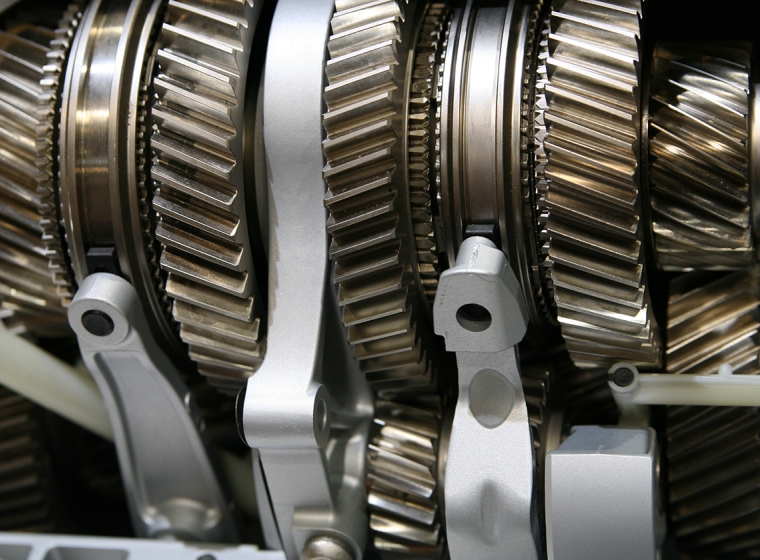
Mechanical Engineering Support for Dispute Resolution
Mechanical engineering support and testimony for litigation, international arbitration, mediation, and insurance.
Experts
Our global and comprehensive expertise across industries gives us a deep understanding of current challenges, best industry practices, and the implications of emerging technologies.
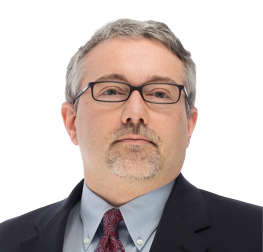
Practice Director and Principal Scientist

Practice Director, Director of Asia Offices and Principal Engineer

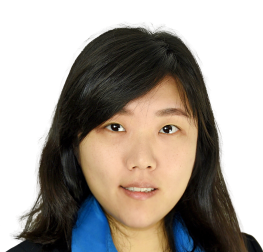


Principal and General Manager
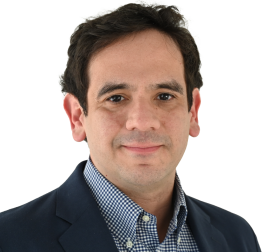
