Breakthrough insights into your most complex mechanical failures.
Downtime due to mechanical failure is a vulnerability we all seek to avoid, but when accidents, user-error, or product failures occur, clients turn to Exponent for our robust analysis and support. Modern mechanical systems are highly integrated, and when failures occur, our multidisciplinary engineers and subject matter experts have the experience, tools, and expertise to objectively determine the root cause of your challenge. Our teams conduct computer modeling of highly complex materials, structures, and machines; analyze nonlinear fracture mechanics; perform advanced laboratory testing; and leverage big data to solve the most complex problems involving mechanical failures.
Leverage our data-based approach to solve problems involving mechanical failures.
Modern, complex mechanical systems are often highly computerized and instrumented, recording vast amounts of data during operations. When failures occur, this data often contains essential clues about the cause of failure. Exponent has the expertise, software, and computing power to sift massive databases for data relevant to a failure, analyze the data, and communicate complex results so that they are readily understood.
We evaluate failures due to fractures.
Mechanical failure is often due to fracture of a part of the system. To understand failures involving fracture, Exponent applies state-of-the-art linear and nonlinear fracture mechanics and damage mechanics. Our teams have deep experience with brittle and ductile fractures in metals, plastics, ceramics, biological, and composite materials. We analyze fracture surfaces macroscopically and microscopically, calculate J-integral crack driving forces, and measure crack growth resistance in the laboratory as we seek the causes of mechanical failure. We apply cyclic loads to induce fatigue fracture in the laboratory using servo-hydraulic, electronic, mechanical, and vibratory testing machines, in order to replicate failures that have occurred and prevent others.
Our teams evaluate root causes due to non-mechanical issues.
The root cause of many mechanical challenges involves non-mechanical issues. Exponent's teams apply engineering and scientific expertise from more than 90 disciplines to work together to identify potentially non-mechanical contributors to failures, such as those related to corrosion, polymer chemistry, thermal sciences, human factors, and others.
Capabilities and Services
Our Capabilities Are Unparalleled
With expertise in over 90 disciplines and hundreds of capabilities, tools, and methodologies — we get to the root of even the most complex challenges and give you the objective answers you need.
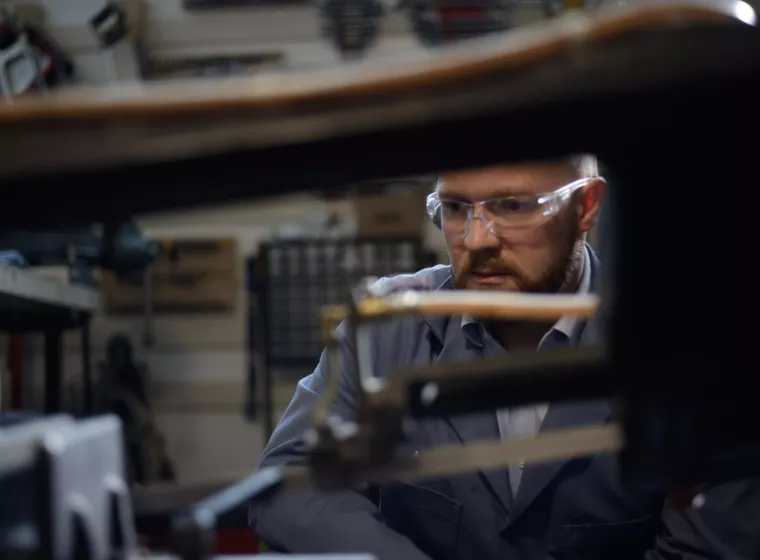
Mechanical Engineering Specialties
Mechanical engineering support to help solve complex problems within commercial and industrial applications.
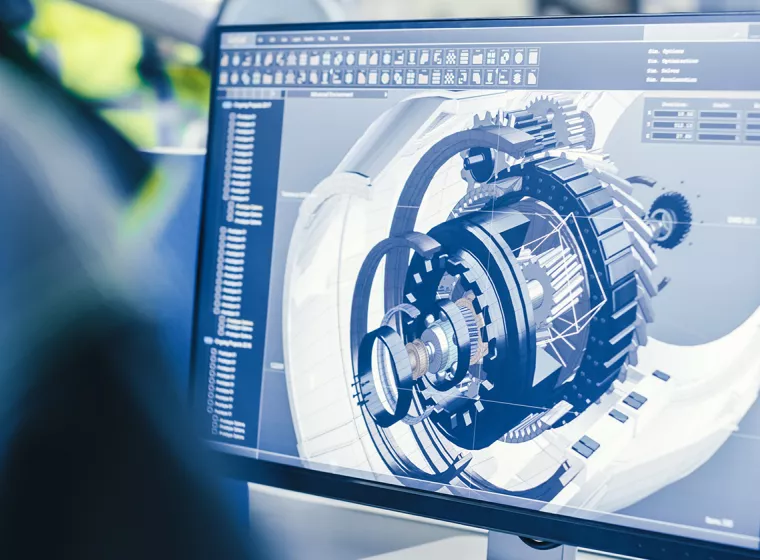
Mechanical Design Support
Mechanical design and testing support services, including customized mechanical modeling, finite element simulations, and system-level testing.
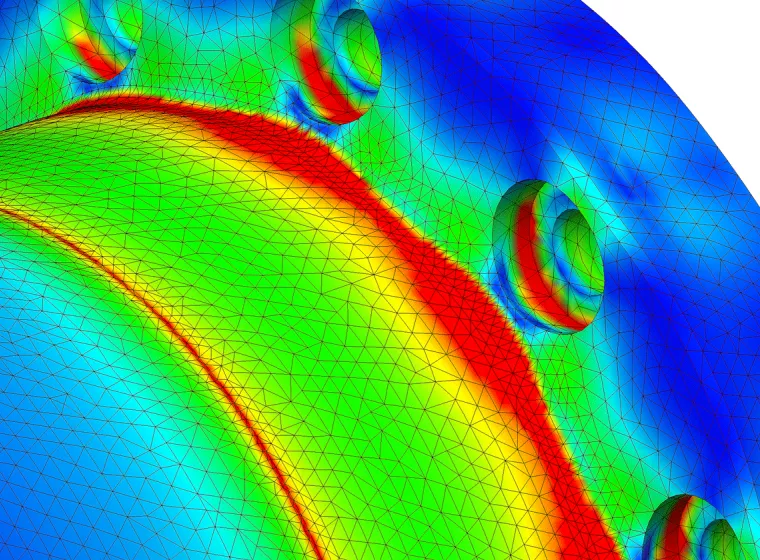
Mechanical Failure Analysis
Discover the root cause of mechanical failure using visual modeling simulation, data analysis, on-site investigations, and laboratory testing.
![Factory Auditing & Assembly Line Evaluations [ME]](/sites/default/files/styles/cards_home_card/public/media/images/GettyImages-1320492982.jpg.webp?itok=yHRcmsIH)
Factory Auditing & Assembly Line Evaluation
Understand highly integrated automated machinery challenges and mechanical problems across diverse industries.
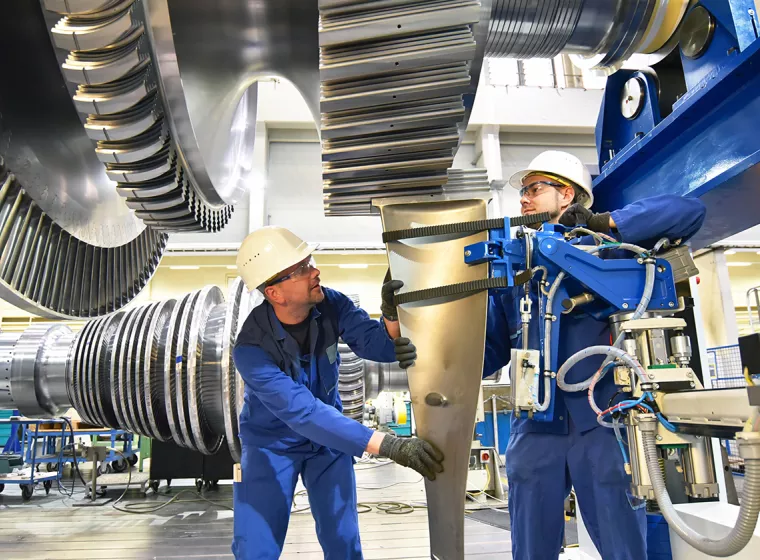
Risk & Safety Analysis for Mechanical Engineering
Multidisciplinary risk assessments, equipment safety evaluations, and occupational safety analysis.
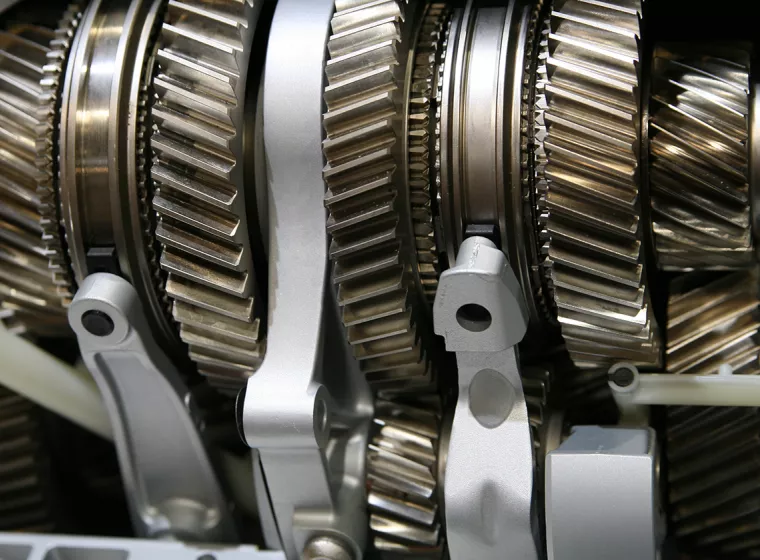
Mechanical Engineering Support for Dispute Resolution
Mechanical engineering support and testimony for litigation, international arbitration, mediation, and insurance.
Experts
Our global and comprehensive expertise across industries gives us a deep understanding of current challenges, best industry practices, and the implications of emerging technologies.

Group Vice President and Principal Engineer
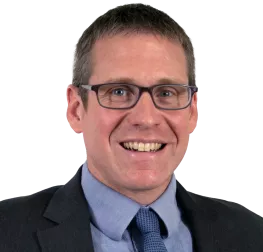
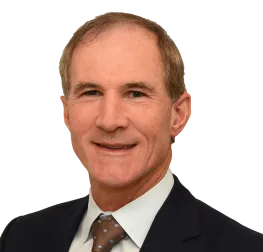
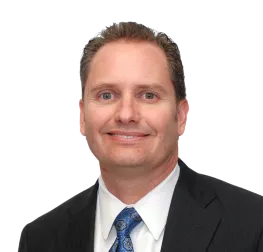

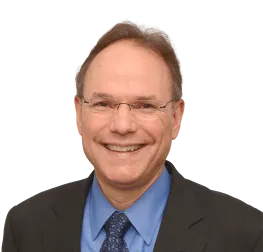
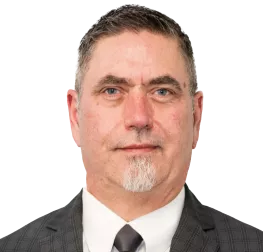
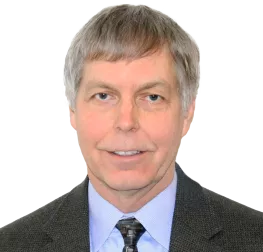
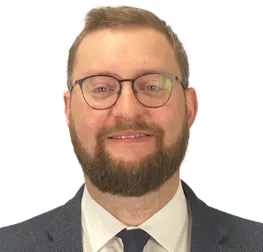
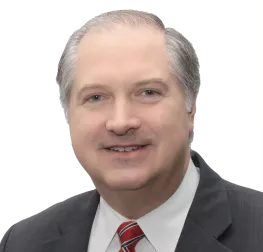
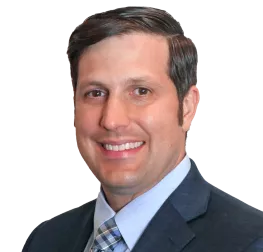
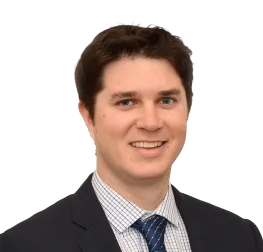
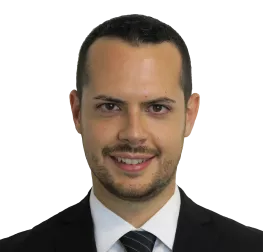
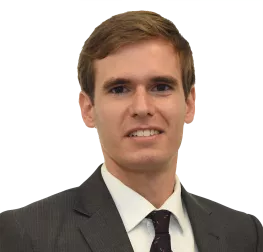


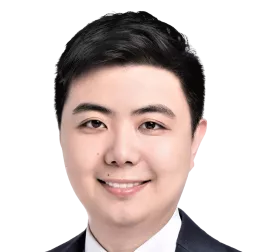
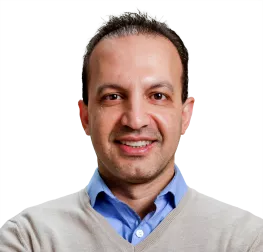
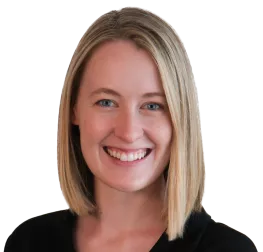
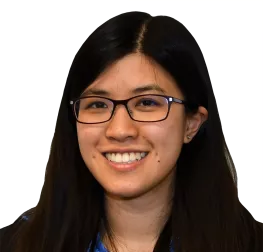

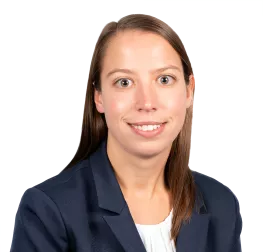
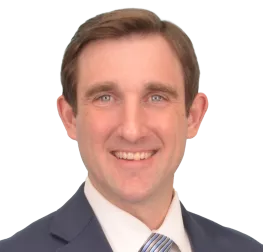

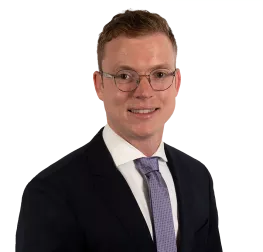
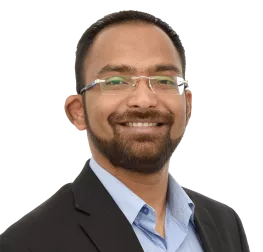
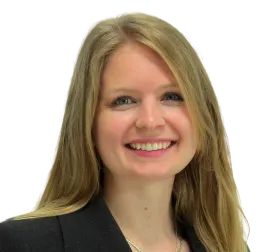


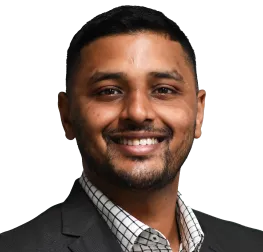
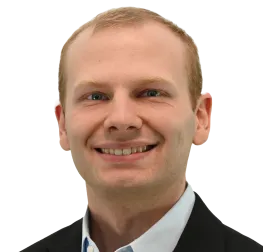
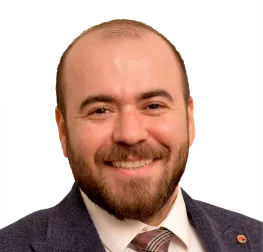
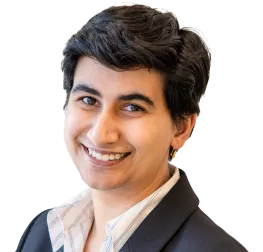
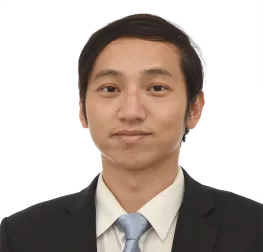
Insights
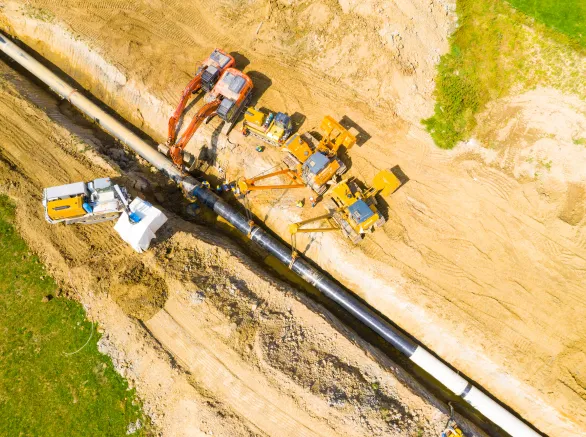