June 16, 2023
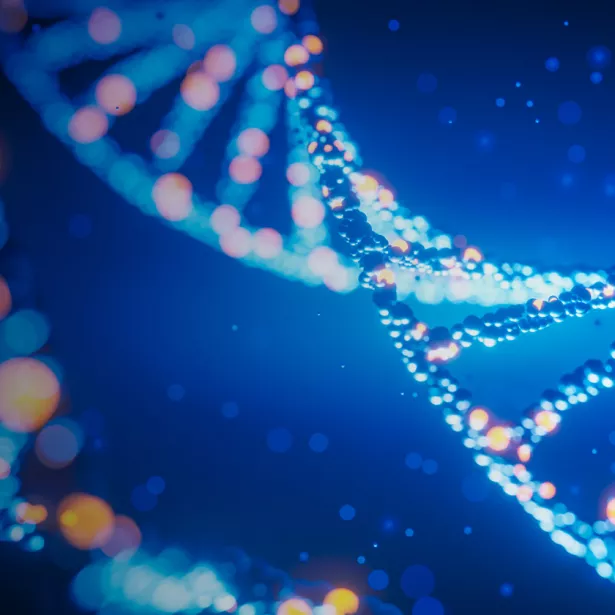
Identifying and evaluating the right battery and supplier for critical applications
Advances in battery-powered consumer electronics have long been enabling innovation in medical devices. As the performance, quality, and reliability of commercial batteries improve, their use in applications ranging from wearables to implantables has become commonplace. Many medical device manufacturers make commercial electronics batteries their first choice for product integration, but while commercial batteries offer significant benefits in cost and time, they are far from plug-and-play.
The demand for battery-powered medical devices continues to grow, with global suppliers producing batteries according to a broad mix of international standards and regulatory requirements. For medical device manufacturers facing stringent requirements, selecting the right commercial battery to meet life-critical product demands is increasingly complex — and can make or break a device's regulatory approval.
Balancing medical device design and battery selection
One of the key differences between consumer electronics products and medical devices is their development cycle. While electronics are largely iterative, with new generations of devices appearing on the market year over year, medical device development cycles are long and complex, with much less tolerance for risk. If a battery-powered medical device doesn't perform as intended, it may be rejected by regulatory agencies after a thorough submission process or worse, recalled after it's on the market. The focus on user health, safety, and quality of life increases the pressure to get it right the first time, starting with product design.
Optimal design of a medical device using a commercial battery is a two-step process. The first step is to reach a point in the design where critical battery parameters such as form factor, power and energy capacity, duty cycle, and lifecycle can be specified. The second step is to identify and evaluate the commercial batteries that can reliably meet those specs before fully completing the device's design. Progressing too far without assessing the available commercial battery options increases the likelihood that a custom battery will be needed. Custom batteries are always an option but are typically very expensive and difficult to produce at scale.
Spec sheets rarely, if ever, give sufficient test information to evaluate whether a battery will work for a medical device application.
Specifications vs. real-world performance
The starting point for evaluating battery performance is the supplier's specification sheet. The spec sheet provides basic information on how a battery will perform under nominal conditions and can be used to establish choices during the design phase. However, spec sheets rarely, if ever, give sufficient test information to evaluate whether a battery will work for a medical device application or meet stringent quality system requirements. Customized testing can help ensure a commercial battery will meet applicable operational, reliability, and safety requirements for the specific end use, all of which are essential for regulatory approval.
In one example case, Exponent performed advanced testing for a medical device that used primary lithium cells in a parallel configuration to power a wearable drug delivery system. It was reported that the cells could be stored up to two years before their use. At first, new cells from five manufacturers appeared to meet the device's minimum operating requirements, and it seemed the medical device manufacturer would have its choice of suppliers.
However, our tests revealed that as battery cells aged during storage, impedance characteristics broadened compared to those of the new cells. Because the battery cells would be discharged in parallel, a mismatch in impedance could result in a higher discharge current in the lower impedance cell, which, in turn, could result in a failure to meet minimum operating requirements. With more stringent testing, we concluded that only one battery supplier met the medical device manufacturer's requirements within a sufficient margin of safety for this critical application.
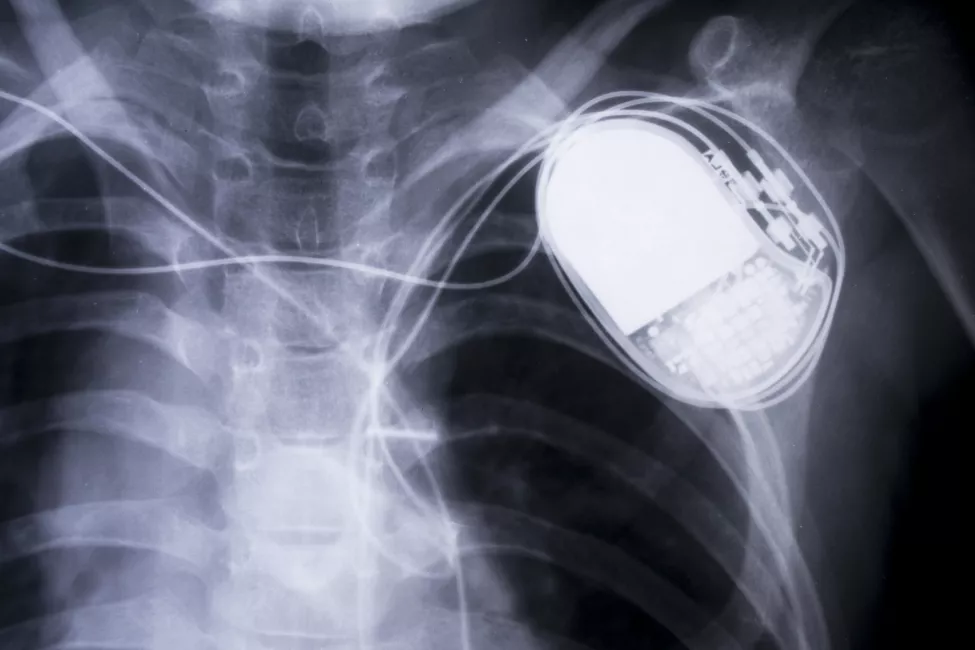
Choosing the right partner
Selecting the right supplier means considering both technical and business requirements. Can the supplier reliably deliver batteries of sufficient quality in the quantities needed? Could manufacturing defects or environmental factors pose risks that increase the chance of failure? Will notification of any changes to the supplier's internal processes or components be communicated?
Verifying the right partner may include auditing the battery supplier's production facility, from incoming quality control, to critical manufacturing processes, to outgoing quality control.
Testing can also help evaluate the quality of the batteries a supplier provides. For example, one study we performed demonstrated the accelerated aging conditions necessary to emulate the effects of the equivalent of multiple years of storage on device performance. Such tests can be used to predict shelf life and inspect incoming cells that have been stored for long periods. Charge/discharge studies are also necessary to fully validate battery selection.
Safety beyond standards
Choosing the right commercial battery for medical device applications is inherently a high-stakes proposition. The standardized safety tests that most commercial batteries must pass are not likely to accurately reflect the risks of a particular medical device application or foreseeable use and misuse conditions. Customized testing and evaluation that reflect a wide range of patient characteristics and use patterns can help ensure that a reliable commercial battery supplier meets the performance and safety requirements for medical device development and regulatory approval.
What Can We Help You Solve?
Exponent's expertise in battery technology for medical devices spans qualification and selection as well as design verification and validation. We can help ensure battery performance, quality, and safety across all stages of medical device design and development efforts for a range of applications and needs.
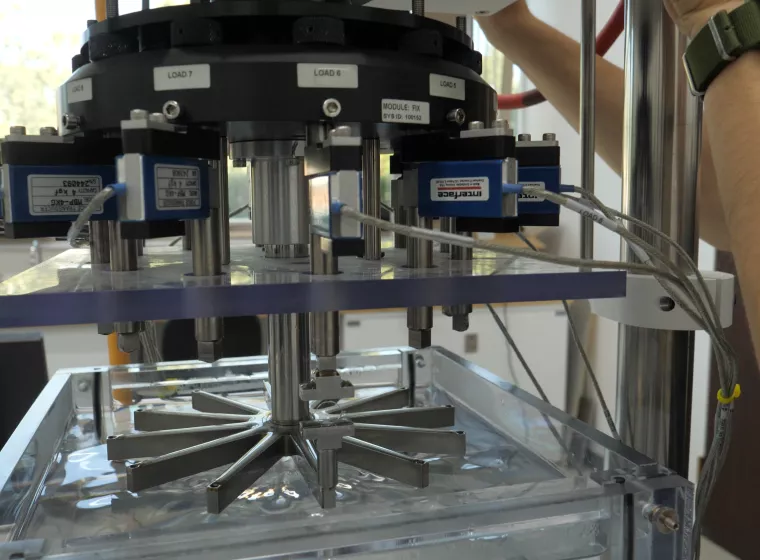
Medical Device Evaluation
Sophisticated medical device evaluations for a vast array of applications.
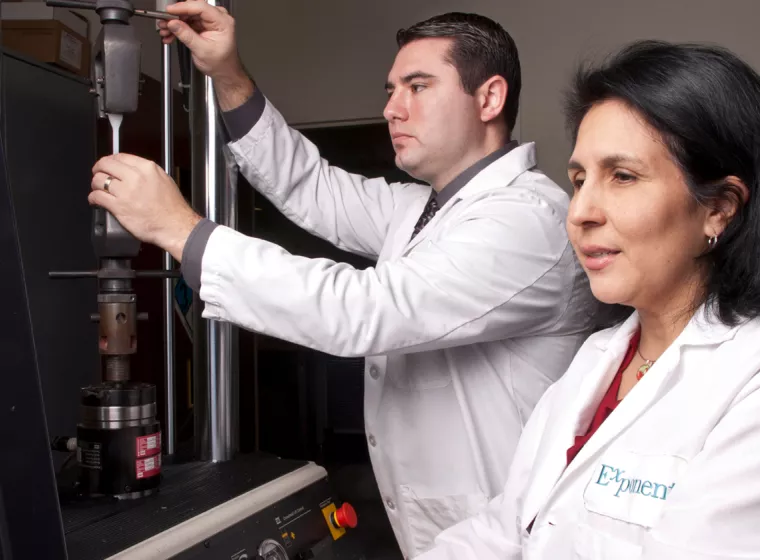
Medical Device Design & Development Support
Crucial medical device design and development analyses to empower your decision-making.
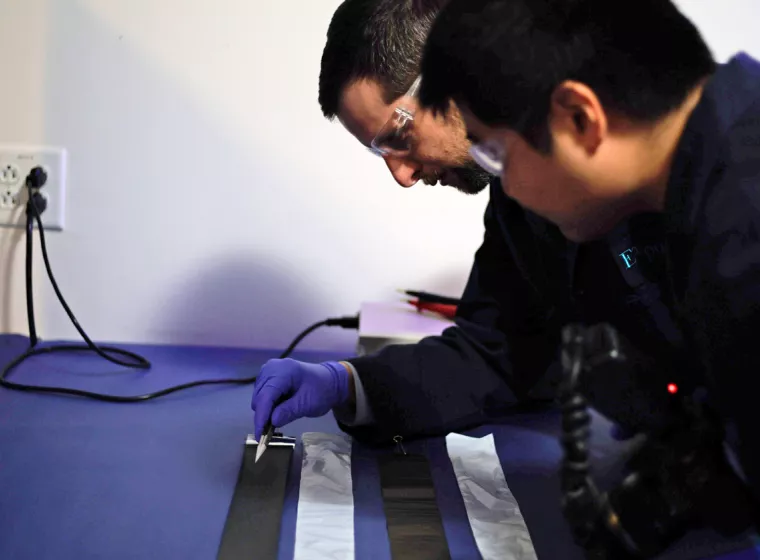
Battery Vendor Evaluation Services
Independent, objective analyses that empower innovative, reliable battery product journeys.
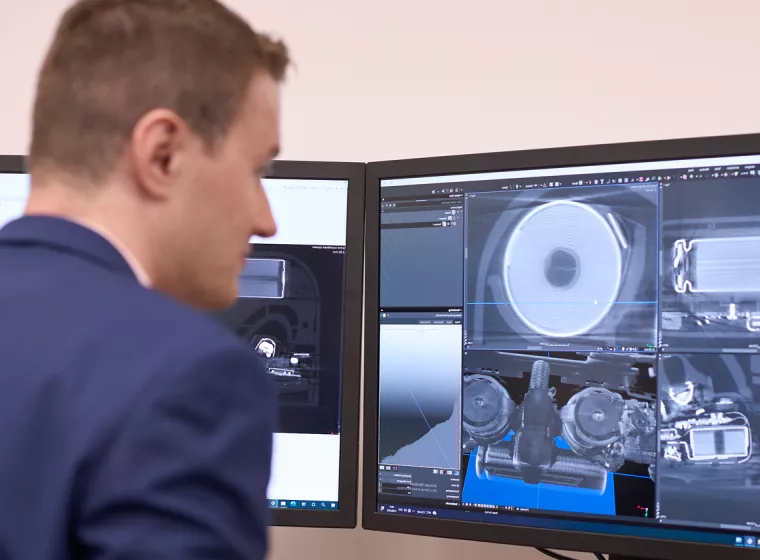
Battery Design Review, Quality & Safety Assessments
State-of-the-art battery design, performance, quality, and safety assessments to support manufacturers' requirements and industry standards.