May 16, 2024
Higher capacity silicon-anode lithium-ion batteries make data-driven insights more important than ever
The world is demanding more powerful, longer-lasting batteries for electronics and vehicles. Many new battery technologies and chemistries are rising to the challenge, from sodium-ion to solid state to lithium-ion batteries with silicon anodes — the market for which is projected to grow by more than 60% over the next 10 years.
The momentum behind silicon-anode batteries is in large part driven by their ability to store more energy than lithium-ion batteries of equivalent mass and volume. However, their increased energy density could also pose new, different, and potentially more dangerous risks in the event of a failure.
While many startup companies and major manufacturers are ramping up silicon anode production, ensuring these batteries can hold up to real-world use is paramount. Gaining and maintaining market share for this emerging technology will take special focus on developing effective safety, reliability, and long-term performance testing.
Capturing benefits, managing risks
Lithium-ion battery chemistry has remained relatively unchanged for decades. In a lithium-ion battery, lithium ions flow between the graphite anode and the transition metal oxide cathode. Graphite is a configuration of carbon atoms in an intricate yet durable honeycomb structure that is resistant to swelling and physical damage, resulting in an anode that is strong and relatively stable during use. This durability is why graphite has been used in commercial lithium-ion batteries since the 1980s.
However, graphite can only hold so many lithium ions: it takes six carbon atoms in a graphite configuration to hold a single lithium ion, which limits the overall energy density of lithium-ion batteries.
In comparison, Silicon can hold 10 times more lithium ions on a per-mass basis than graphite. Silicon anodes may also reduce charge times and increase power output across numerous applications, but there is a critical problem: swelling.
No energy storage system is flawless, but companies can reduce risk and help avoid loss and liability by developing battery testing procedures that go beyond pass/fail results.
Silicon expands to more than three times its original volume when absorbing lithium ions. This swelling is why silicon anodes have remained impractical for many years. Only recently have some companies started developing engineered solutions to control the problem. In some instances, battery firms have completely redesigned the anode using proprietary materials or novel configurations of existing materials, including success in lab testing and plans to move forward with large-scale manufacturing. However, since most of the technologies are still emerging, many have not been subjected to extensive real-world use, increasing the importance of thorough testing for this new chemistry.
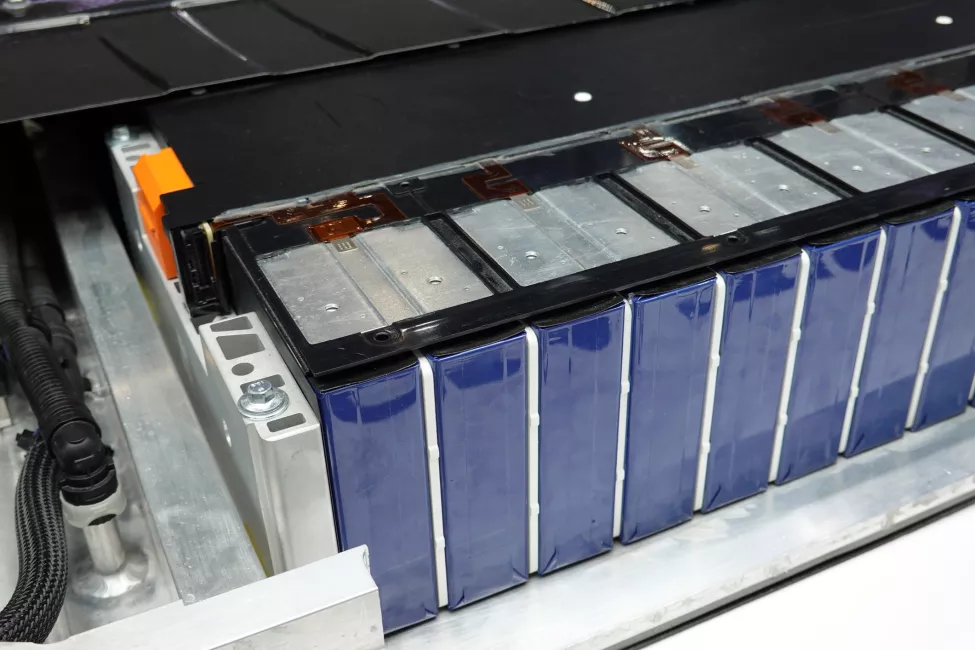
New batteries, new battery testing
When lithium-ion batteries fail, they can release a tremendous amount of energy quickly, potentially resulting in thermal runaway events or fires. Given the higher energy density of silicon-anode batteries, however, thermal runaway events could be even more damaging to devices and dangerous for consumers.
Exponent's abuse testing of lithium-ion cells containing varying levels of silicon supports this concern: as the capacity of cells increases, so too does the severity of the thermal runaway event due to the higher energy content. Preventing cell-to-cell propagation in larger multicell packs and containing sparks and flames in consumer electronics is already a challenge for many device designers. The increased energy from silicon-anode cells only makes the problem more difficult. To address this issue, manufacturers can benefit from not only testing their new battery technologies but also carefully thinking through their applications — both intended use and potential misuse scenarios — to help prevent thermal runaway events and mitigate damage when a failure does occur.
Exponent Licenses FTRC Tech from NASA to Advance Battery Failure Characterization
Silicon anodes also pose new challenges for assessing performance and reliability. Our experience with prototype batteries containing silicon anodes suggests that traditional aging mechanisms can sometimes result in new failure modes. For example, certain 18650-format cells may experience mechanical deformation of their windings into the free space inside certain cell designs as they age, and cell cans can crack open due to the severe expansion of the anode, exposing the internal contents and resulting in leakage of the electrolyte and immediate cell failure.
While any new battery technology will need new testing techniques and protocols, tests for silicon-anode batteries will need to account for higher energy density, novel case materials, updated software, and more. Particularly for evolving technologies and untested applications, building a robust testing regimen can benefit from multiple perspectives, including battery engineers, thermal science specialists, electronics experts, chemists, and materials scientists.
Slow and steady wins the race
Many battery startups and even established manufacturers may be tempted to rush silicon-anode batteries to market for EVs and consumer electronics. There could be significant risk to hastening new, more powerful battery technologies. The market has seen many companies issue costly recalls for devices that weren't truly ready for consumer use and foreseeable abuse.
Due diligence is always important in battery manufacturing, but large leaps in battery technology make it more important than ever. Manufacturers can benefit from understanding unexpected new failure modes and reevaluating their prior assumptions and conclusions about tests. No energy storage system is flawless, but companies can reduce risk and help avoid loss and liability by developing battery testing procedures that go beyond pass/fail results to fully scope potential limitations in performance and reliability.
What Can We Help You Solve?
Our battery and energy storage experts can step in at any point to address specific issues or serve as a partner of choice for battery product development and testing. Our work encompasses industries including medical devices, consumer products and electronics, automated and electric mobility, and grid-scale utilities/energy storage.

Batteries & Energy Storage
Supercharge performance, reliability, and safety across all stages of the battery and energy storage product lifecycle.
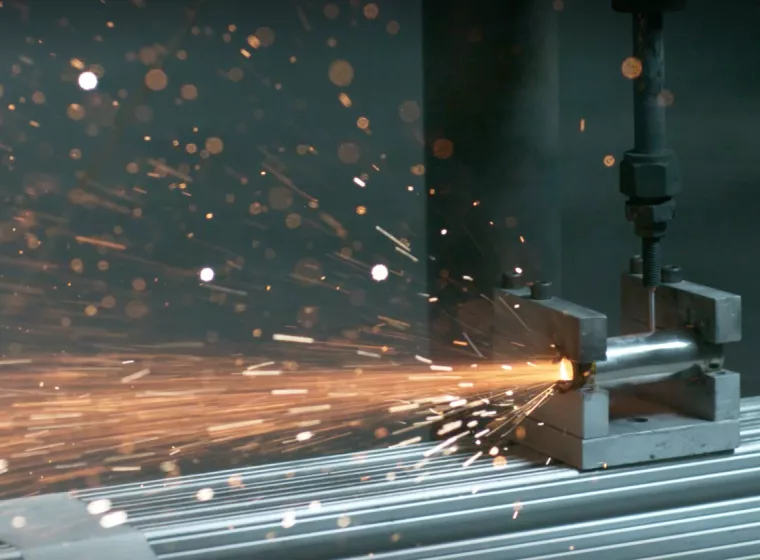
Battery Failure Analysis & Investigation
Comprehensive battery failure analysis to determine the root causes of failures and identify opportunities for mitigation.
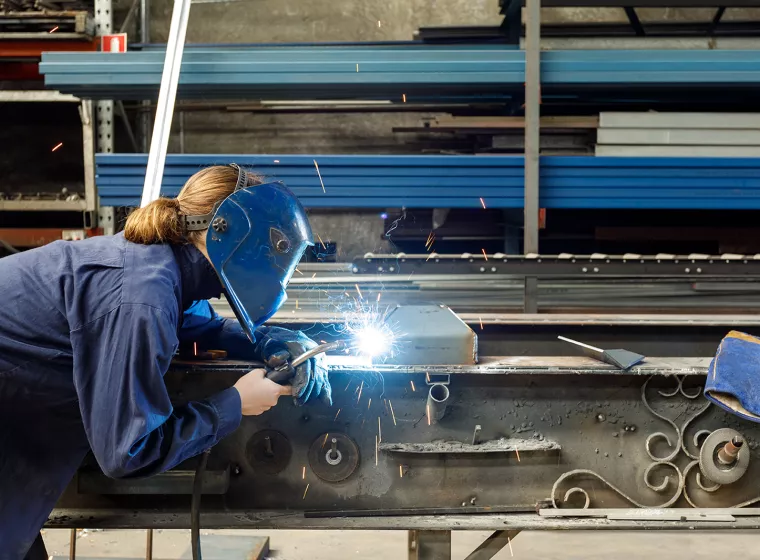
Product & Process Advisory
Materials and corrosion engineers assist with materials issues at every stage of your product or process lifecycle.
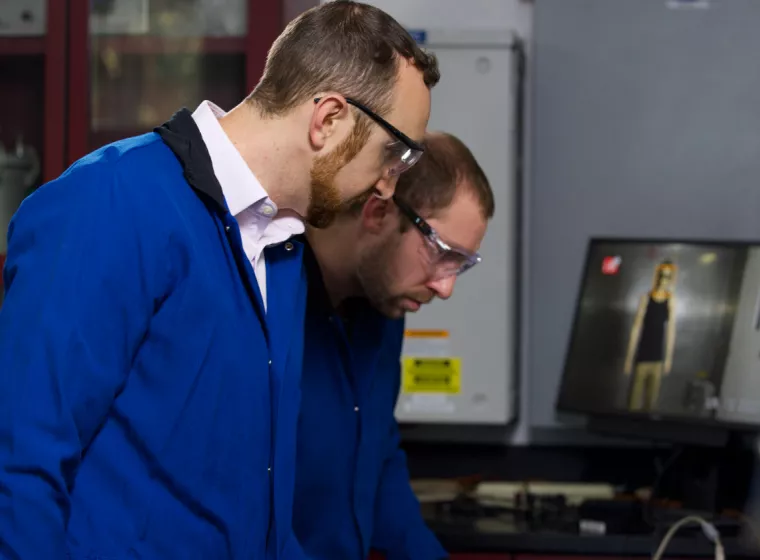
Battery Safety & Recall Support
Support for foreseeable use and misuse scenarios, industry and product requirement evaluations, and incident prevention.
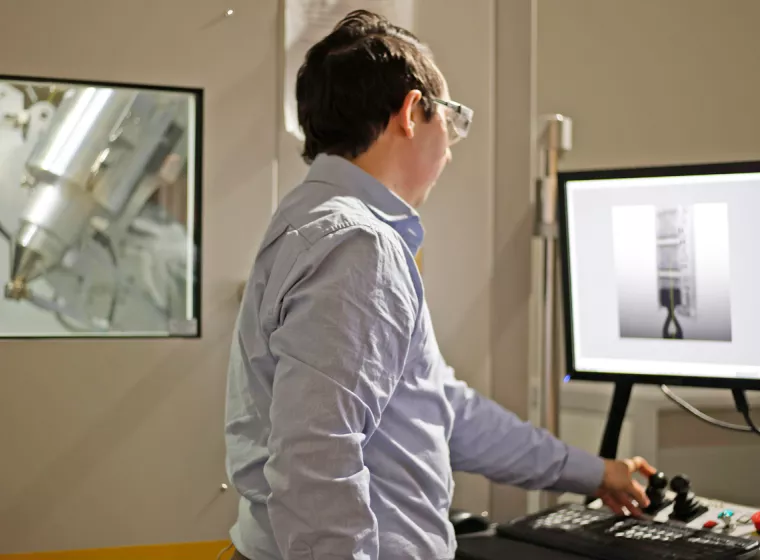
Custom Battery Testing
Custom product safety, performance, and industry certification battery testing services.
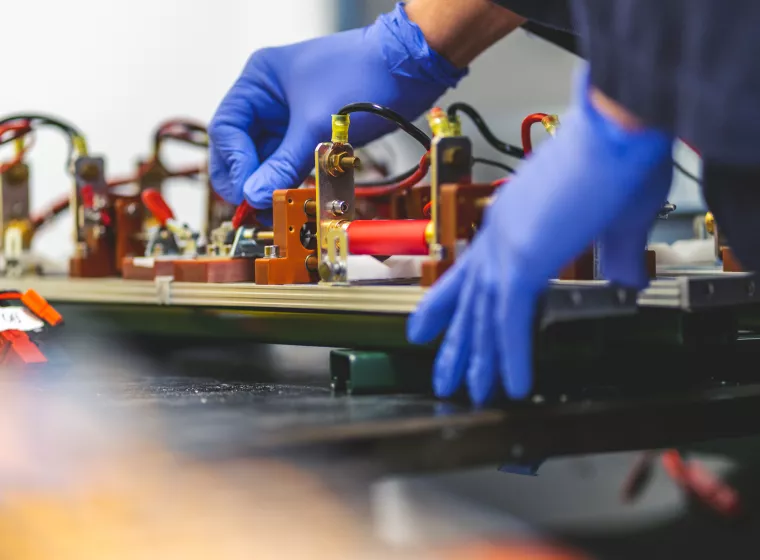
Battery Risk Assessments & Corrective Action
Li-ion battery risk assessment and corrective action services, including cost-effective tools for long-term monitoring.