June 30, 2025
What are the benefits of incorporating human factors principles across the consumer product lifecycle?
In 2020, the U.S. Consumer Product Safety Commission (CPSC) and Health Canada's Consumer and Hazardous Products Safety Directorate (Health Canada) published Guidance on the Application of Human Factors to Consumer Products, stating, "Many product-related injuries can be prevented by better design. Providing the consumer product industry with suggestions on how to apply human factors principles to their products can help lower the number of product-related adverse incidents and reduce costly compliance and enforcement actions."
Since the release of the guidance, recalls and product safety warnings have been increasing steadily from 2020, with a 40% increase in 2024 relative to 2020, and numbers for 2025 are over 75% of last year's total less than six months into the year. In May, the CPSC announced it served 28 product safety recalls and warnings to companies in a single week — more than double the agency's previous high. During a time of changing leadership at CPSC, with questions surfacing about its future, the record-setting news was accompanied by the statement that since the recent presidential inauguration, "CPSC has renewed its focus on its core mission: protecting American families."
Human factors evaluations can and do play a huge role in a product's safety and effectiveness in the market. CPSC does not report on any associations between product recalls and specific testing or guidance that was missed; however, the CPSC website lists multiple recalls for infant and children's products and toys, exercise equipment, safety items for older adults, electronics, and more, with justifications related to use and design.
Despite the CPSC and Health Canada guidance being released five years ago, it's likely that many global consumer product manufacturers may be unfamiliar with the nuances of applying it to their products. Many designs that were in ideation or development in 2020 may just now be reaching the point of postmarket surveillance and consumer reviews. This means stakeholders ranging from product designers and engineers to executives and legal staff are newly grappling with what CPSC and Health Canada's recommendations mean in the context of real-world human factors strategies — and potential recalls.
Human behavior is not only difficult to predict with any meaningful accuracy but subject to countless circumstances and contexts that can have a substantial impact on outcomes.
Manufacturers are also being challenged by uncertainty in the agency's short- and long-term enforcement strategies, with many unknowns about how safety warnings and recalls could progress in the current regulatory climate. The CPSC and Health Canada guidance shares similarities with human factors requirements from agencies like the Food and Drug Administration, the Federal Aviation Administration, and the European Medicines Agency, as well as international standards organizations such as ISO — but whereas those entities govern heavily regulated industries, consumer product manufacturers operate in areas that tend to be grayer with respect to standards and requirements, with little to no formal premarket regulatory enforcement. This means product testing can vary widely, and the manufacturer is responsible for determining what type and depth of testing is appropriate. As one example, an Exponent client conducted numerous premarket safety tests on a product with an integrated blade but did not consider deliberately testing for incorrect product use, with the goal of identifying specific risks associated with potential injury or death and a plan to mitigate them. Exponent, being aware of the CPSC and Health Canda guidance, raised such testing as a consideration resulting in more robust safety testing frameworks, and reduced risk of potential recall related to the incorrect product use tested.
In the event of a recall or injury claim, product developers may need to demonstrate a product's safety profile and show how they evaluated risk. Human factors evaluations offer multiple benefits, including helping manufacturers get ahead of potential regulatory action or recalls and optimize product experiences for users. A critical challenge is translating broad regulatory guidance into meaningful action — and defining those actions at specific points in the total product lifecycle when designers can integrate changes smoothly.
The CPSC and Health Canada guidance framework
For consumer product manufacturers, establishing when human factors evaluations can or should be incorporated into development is important to go-to-market planning, costs, and overall strategy. When evaluations are performed without consideration of the overall product lifecycle, such as conducting user experience testing in parallel with production rather than early on in the design phase, the impacts can be substantial, including costly redesigns, discarded inventory, retooling manufacturing equipment, or even pulling a product from development because known adverse impacts could increase the risk of a recall. Unsurprisingly, CPSC and Health Canada (as well as other agencies) stress implementing human factors evaluations early through preliminary analyses (see Figure 1) to identify (1) product users, (2) critical user tasks, (3) the use environment, and (4) the interaction between user and product design.
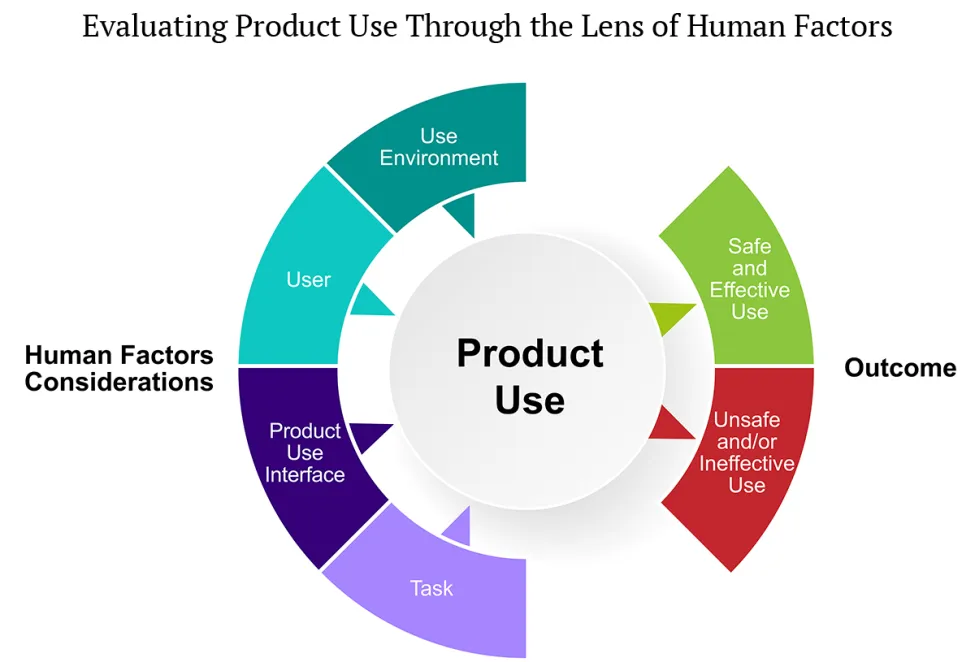
In addition to timing considerations on performing human factors evaluations, consumer product manufacturers must also decide what to evaluate and how to evaluate it, which can be complex challenges. The CPSC and Health Canada guidance specifies the need to evaluate hazards associated with "unintended-but-foreseeable" use and users. This means considering users who may interact with a product in ways the manufacturer did not intend but can "reasonably be expected to occur," as well as users who interact with products that were not designed for them — like children using adult exercise equipment.
As a starting point, the CPSC and Health Canada guidance identifies factors for manufacturers to be aware of in evaluating unintended-but-foreseeable use scenarios. These include:
- Scenarios where a product demands physical, perceptual, or cognitive abilities that exceed those of the intended users;
- When a product's functionality does not match user expectations; or
- When environmental conditions impair user safety.
However, even with the criteria above, human behavior is not only difficult to predict with any meaningful accuracy but subject to countless circumstances and contexts that can have a substantial impact on outcomes. It's important to think critically about how human characteristics, capabilities, and limitations might influence use throughout the design process to accommodate a range of aptitudes, experiences, and use conditions. For example, we worked with an automotive manufacturer to help assess and evaluate different ways that children could access their key fob product, specifically the batteries inside of it. Our human factors consultants leveraged historical knowledge of this product type and proposed a methodology to evaluate the fob's current design for risks to children. From there, we were able to provide insights into the product's design and mitigate risk.
When unforeseen use concerns arise, this is likely to suggest evaluating or testing a product — also referred to by the CPSC and Health Canada as "foreseeable-use analysis" — for all critical tasks (both frequent and infrequent) among diverse user groups. Conducting multiple test sessions or repetitions, as needed, can also be helpful in reducing bias in the evaluation process. One common consideration for consumer products is how strength and dexterity change with age, introducing potential obstacles to operating products (e.g., child-proof packaging may effectively prevent harm to children while at the same time preventing a senior user from accessing medication easily). Visual and auditory capabilities also change with age, which can similarly affect the development of product feedback like alarm lights and sounds. Particularly when incorporated early in the design process, findings from these evaluations can directly inform functional product decisions, the scope of intended users, warnings and labels, and more.
Beyond testing, methods for identifying "unintended-but-foreseeable" use scenarios can include reviewing historical or public data sources involving the product or similar products for consumer complaints, product reviews, recall information, injury databases, and more. These considerations are often implemented proactively but can provide important answers for companies facing safety warnings or alleged incidents in determining the next steps to satisfy regulatory inquiries.
Human factors and real-world implementation
A primary goal of incorporating a human factors evaluation is to support safe and effective product use "without serious use errors or problems," per the CPSC and Health Canada guidance. Once reasonably expected product uses are identified, a thorough risk assessment can help determine, prioritize, and mitigate potential use-related hazards. In considering risk assessments, however, it can be useful when the outcome data amount to more than abstract ratings about the likelihood of an event occurring. An approach that synthesizes behavioral science and engineering analysis to quantify hazards through domain-specific characterization offers a robust understanding of foreseeable use and use-related challenges.
For example, when a manufacturer came to Exponent with product failure complaints in the field, we conducted a human factors evaluation that identified patterns of use scenarios, ultimately identifying the root cause of the failure. In parallel, Exponent's materials engineering experts replicated those conditions in a lab environment to determine the direct cause. Findings from the integrated human factors and materials engineering experts enabled the manufacturer to define and implement design changes that not only impacted the product in the field but subsequent products in development as well.
Connecting the total product lifecycle
Human behavior is variable and context-dependent, making it difficult to predict with complete accuracy. As a result, even well-intentioned designs can lead to product recalls, costing companies time, money, and reputational damage. To support safety and effectiveness once a product is on the market, post-production reviews and postmarket surveillance can be powerful tools for identifying issues that may ultimately lead to incidents. This includes use by inappropriate user groups or in unexpected environments (e.g., indoor use of outdoor products).
As CPSC guidance and the regulatory landscape that influence product safety and recalls evolve, expert human factors evaluations will continue to be supportive in both avoiding and responding to consumer insights, incidents, and recalls. By integrating human factors evaluations throughout the product lifecycle, from assessing early concepts and refining current designs to leading usability studies and supporting recall mitigation, human factors experts help uncover potential use-related issues before they become costly problems. A user-centered perspective not only enhances usability but also improves product safety and regulatory outcomes. When applied effectively, human factors insights can improve product safety, usability, and regulatory compliance. Yet integrating human factors isn't always straightforward: organizations must navigate constraints like limited timelines, evolving user needs, complex use environments, and internal alignment around user insights. Addressing these challenges early and consistently will help in building safer, more effective products.
What Can We Help You Solve?
Exponent's engineers and scientists have extensive experience evaluating hazards associated with the use and misuse of a wide array of products. We leverage publicly available data, scientific literature, regulatory knowledge, and domain expertise to identify hazard patterns and develop and conduct tests with volunteers and anthropomorphic test devices to assess product usage and injury potential.
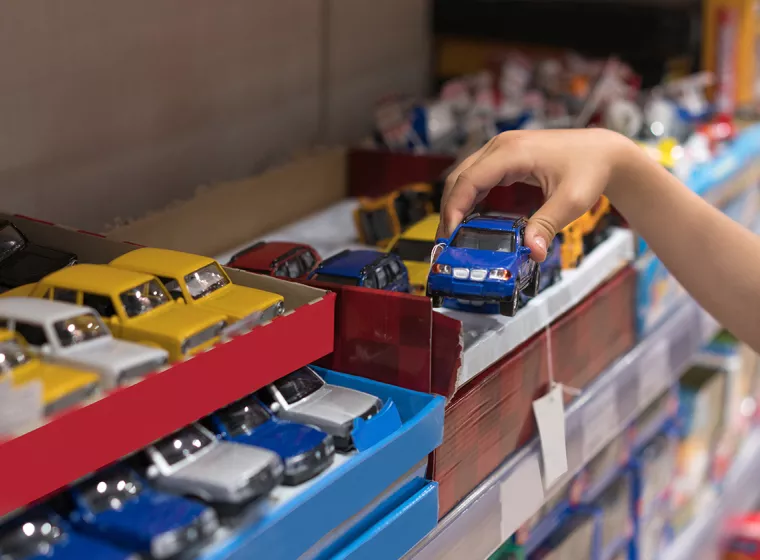
Consumer Product Design, Usage & Injury Analysis
Expert user interaction analysis to support mitigating the risk of injuries from consumer products.
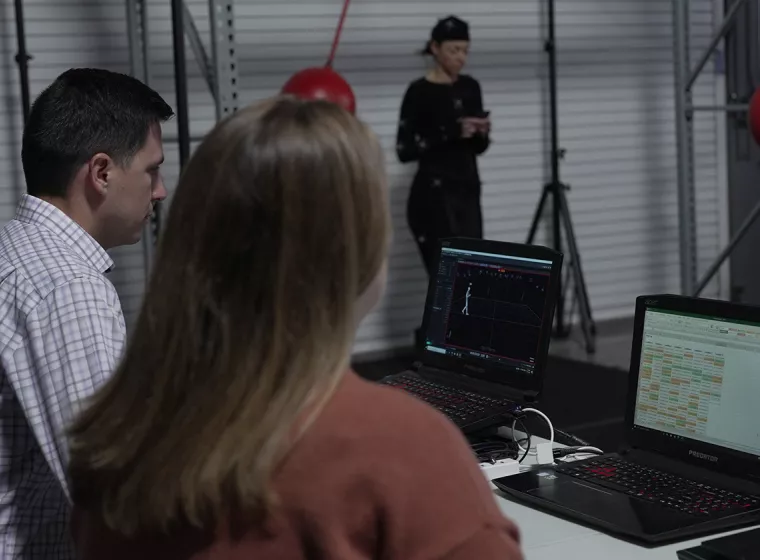
Improve User Research & Testing
Human factors investigations for data-driven product and process design decisions.
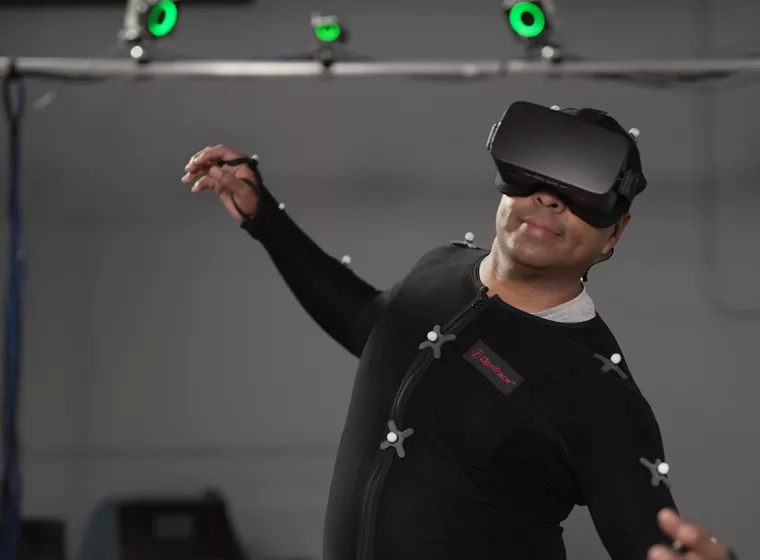
Product Design & Safety
Human factors and risk analyses to help clients improve designs for a range of products.

Child Safety
Understand the impact of various products on child safety with expert human factors analyses.
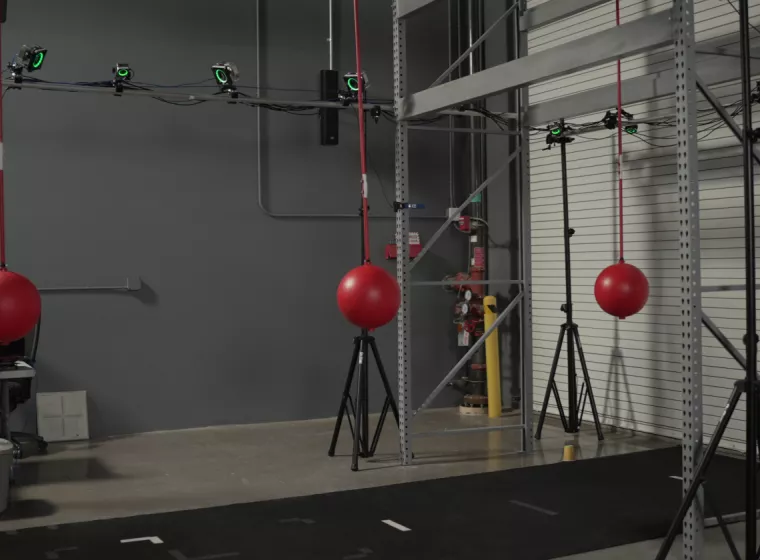
Cutting-Edge User Research Testing & Evaluations
Pioneering scientific user experience research across the full lifecycle of consumer, industrial, automotive, and medical device products.
Insights
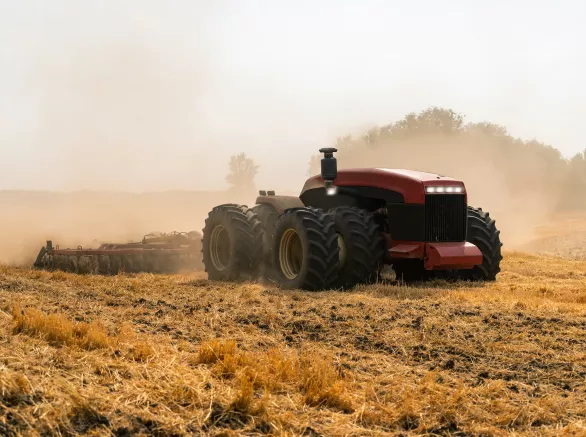