September 9, 2021
Exploring the benefits of one-of-a-kind mechanical testing solutions
When shared e-scooters appeared on city streets in 2017, even the minimum testing standards and safety regulations that e-scooters need to meet had not been developed. Even though around 50 shared e-scooter brands are now in service in hundreds of cities worldwide, safety standards specifically governing e-scooters are still being developed — especially for rental use. As a result, scooter companies are finding it challenging to evaluate the quality, safety, and lifetime durability of their products.
Without fully developed standardized testing guidelines, designers and manufacturers of rental e-scooters have devised customized protocols and tools that simulate end-use conditions, accelerated aging, and foreseeable misuse, so they can design their e-scooters to mitigate potential safety concerns for heavy usage, rough handling, and vandalism.
For example, by applying customized testing for heavy usage, such as curb drive testing, drop testing, and impact testing (to mimic vandalism), designers can determine whether they need to adjust the structural design, select a high-strength material, or use more material to improve product safety by making the product more resistant to external loads.
As the e-scooter example shows, by detecting potential problems early in the product development lifecycle using customized methodologies and tools, companies can improve product design and durability. However, knowing how and when to use customized testing requires specialized knowledge.
One-of-a-kind mechanical testing
Because demand for accurate design review, quality assessment, and failure analysis/failure re-creation during the product lifecycle is increasing, customized testing is becoming more essential to supplement standardized testing.
However, unlike standardized testing, which follows well-defined, detailed protocols and industrial guidelines, customized testing requires knowing how to design non-standardized methodologies to assess a product's foreseeable operational misuse. It also requires identifying when a thorough risk assessment using customized testing is most valuable, as the following three situations show
Analyzing Products Under Simulated End-Use Conditions
Customized end-use testing can help optimize the design, safety, quality, and reliability of new products, when there are no well-developed standards and regulations. End-use testing can include analyzing the structural strength of a scooter by driving it from the sidewalk, over the curb, and onto the road; driving on different surfaces; or simulating potential rider hazards using dummies.
For example, to test the stem strength of e-scooters, a customized stem force tester (Figure 1) was designed to accurately mimic how riders cyclically push and pull the handlebar. The loads and cyclic frequency were determined in separate, live road tests, which helped optimize the stem design and provided more efficient, controlled testing.
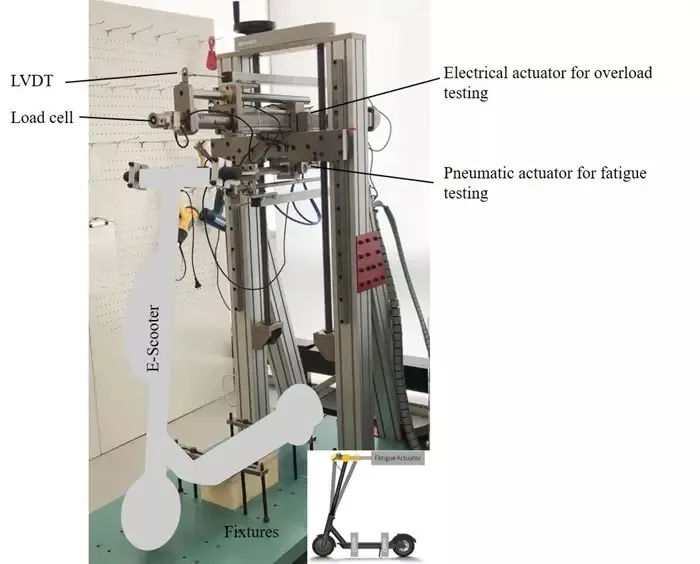
Figure 1. E-scooter overload/fatigue testing.
Testing Unwieldy Components or Systems
Many consumer products have unwieldy components that are difficult to study using standardized methods, especially in the electronics, medical device, and battery industries.
Combining conventional and customized testing and tools can allow the material, structural, and performance properties of these "untestables" to be analyzed on micro- and macro-scales more effectively.
For example, a customized mini-universal test rig was designed for conducting battery abuse testing at 100% state of charge in a conditioned environment. To determine the strength of the battery material, 3-point bending and indentation were applied to the battery material (Figure 2) in an environmental chamber, allowing the resistance of the battery material to bending and indentation to be measured precisely.
After accurately measuring cell flexural stiffness and local hardness, battery designers used this data to apply calibrated numerical simulations to investigate the effects of load and deformation on the battery's structure more cost-effectively than testing multiple prototype designs.
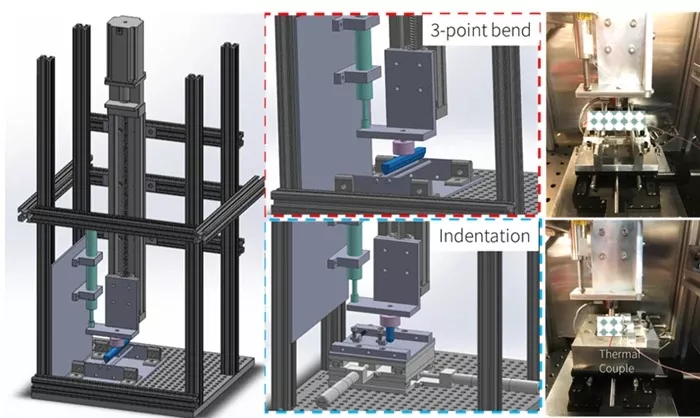
Figure 2. Battery abuse testing (3-point bending/indentation).
Re-creating Failure
To improve the robustness of product designs, product makers may seek to understand how products may fail under use conditions not reflected in the existing standards. Failure modes and effects analysis (FMEA) is often used to reduce failures when bringing a product to market. During FMEA, failure replication testing can help identify relevant and realistic failure modes and effects by recreating product failures in a consistent, controlled manner.
By using customized, statistical design-of-experiments (DOE) and computer simulations, designers and manufacturers can study the effects of multiple foreseeable use and misuse scenarios to design products that are less likely to fail or less likely to cause severe consequences in the event of a failure.
When used in conjunction with standardized testing, customized testing can also help designers and manufacturers supplement failure analysis to validate failure root causes and isolate complex failure modes.
For example, as part of the risk assessment for a computer touchpad, customized equipment (Figure 3a) was constructed that allowed designers to characterize keyboard contact failures due to contaminants from simulated skin and food oils. Using a similar apparatus (Figure 3b), designers were also able to simulate touch-sensing unit cracking due to excessive user load by mimicking finger pressure.
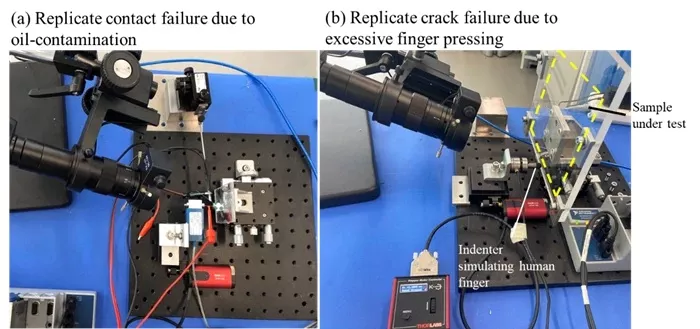
Figure 3. Failure replication. (a) Contact failure replication induced by oil contamination; (b) Touch-sensing unit cracking replication due to excessive finger load.
In the future, customized testing may not only enable more complex consumer products to successfully go to market but may also help establish new standards and guidelines where there are currently none.
How Exponent Can Help
While customized testing methods can help mitigate product quality concerns by identifying potential design risks and isolating complex failure modes, these methods require specialized expertise and fully understanding of the product from the material and structural perspectives. Exponent's multi-disciplinary team of mechanical engineers and materials scientists has extensive experience in customized testing, design review, and risk assessment. Through our custom methodologies and tools, we can detect potential problems early in the product development lifecycle to help ensure usability, manufacturability, and reliability before a product is introduced to the market.