September 23, 2021
Recent sustainability initiatives in the chemical industry
The chemical industry converts raw materials into some 70,000 different products needed for everyday life. Many of these products are not recycled, rather they are produced in ways that emit greenhouse gases (GHGs). With growing societal concern over climate change and waste, some end-users, environmental groups, and financial institutions are demanding greener products and manufacturing practices.
Due to increasing pressure to promote sustainable business practices, the chemical industry is focusing on three sustainability initiatives: (1) reducing GHG emissions, (2) reducing plastic waste, and (3) using more renewable raw materials such as biobased feedstocks.
The chemical industry's ongoing transition to more sustainable practices involves technological and legal risks.
By carefully considering all three initiatives and their challenges, stakeholders can mitigate risks while developing a sustainability plan that is appropriate to each company's unique situation.
Reducing GHG emissions
Because certain chemical manufacturing processes emit large quantities of CO2 and other gases with greenhouse warming potential (e.g., nitrous oxide and methane), many companies are committed to identifying GHG reduction opportunities using the Scope 1, 2, and 3 methodologies, as defined by the U.S. Environmental Protection Agency.
While Scope 1 refers to direct GHG emissions and Scope 2 covers indirect emissions from utility usage, Scope 3 includes all remaining indirect emissions related to operations. This includes GHG emissions from methane leaks during production, the transportation of fossil hydrocarbons, and product disposal, among others. For most chemical manufacturers, Scope 3 constitutes the largest source of emissions.
To reduce these emissions, companies are considering several approaches. One such approach captures and sequesters fugitive carbon to limit CO2 emissions to the atmosphere. Companies may also use alternative chemical production routes that emit less harmful or reduce GHG by-products. Chemical companies are also attempting to decarbonize their energy inputs by relying more heavily on renewable power, including solar, wind, and hydroelectric.
As with any new technology, these approaches carry risks. One key challenge in carbon sequestration is preventing carbon from escaping into the atmosphere. Companies pursuing new production pathways may face unexpected additional R&D spending or lower-than-expected plant or product performance.
Manufacturers leveraging renewable power accept the risk of its intermittency, potentially leading to unforeseen plant shutdowns. Plant stoppages can lead to considerable economic damages due to lost revenue, large costs to fix deficiencies, and penalties for unfulfilled supply or acceptance contracts while exposing technology suppliers and engineering, procurement, and construction (EPC) firms to litigation.
To reduce these risks, manufacturers can add redundant equipment and perform the proper scale-up by testing new technologies on a smaller scale. Also, stakeholders using renewable power should consider setting up contracts with utility companies that provide enough flexibility to mitigate the risk of power outages or installing energy storage systems or backup power generation to at least cover brief interruptions.
Preventing plastic waste
Since the first large-scale use of plastic in the 1950s, more than 8 billion metric tons of plastic have been produced globally. Of the 8 billion metric tons, about 6.3 billion have become waste. When properly formulated, collected, sorted, and processed, most current plastics can be recycled into new plastic products, in principle. In practice, however, recycling plastic waste involves many challenges, including incorporating recycled material into new products and a lack of economic incentives.
Plastic manufacturers are overcoming recycling obstacles through intentional redesign, while other companies are using chemical recycling technologies that can overcome many limitations of current mechanical recycling processes. Another approach to reducing plastic waste involves incorporating recycled material into new products, such as producing resins with recycled content. In part, state-imposed minimum recycled content requirements on packaging materials are driving this approach in the U.S.
However, regulatory restrictions and performance specifications may limit the use of recycled material because it has the potential to introduce unforeseen hazards and product defects. For example, FDA regulates the use of recycled plastic in food applications and medical products and requires manufacturers to demonstrate that possible contaminants from prior use of the plastic have been removed by the recycling process.
Using biobased feedstocks
For more sustainable manufacturing, the chemical industry is working to replace fossil feedstocks — raw materials derived from carbon-based compounds, like oil and natural gas — with biobased feedstocks from renewable raw materials, such as sugars, plant oils, or lignocellulosic (plant matter) biomass. However, biobased feedstocks are more expensive, have higher feedstock variability, and are much less stable than traditional fossil-based feedstocks.
To overcome the higher cost of biobased feedstocks, companies can either slowly ramp up production to match demand or follow a mass-balance approach. The mass-balance approach tracks all intermediate products derived from a mixture of biobased and fossil feedstocks in a value chain. Based on the feedstock ratio, a fraction of the end-products is labeled as made from biobased feedstocks. Increasing production slowly can be more capital intensive because multiple manufacturing plants must often be built. Using a mass-balance approach can also be problematic.
Customers and other end-users may question or challenge the made-from-biobased-feedstocks claim on the end product because both biobased and fossil feedstock were used in the production process. These challenges could lead to disputes or a damaged reputation if the customer views the company's actions as greenwashing.
Owing to the greater variability and instability of biobased feedstocks, chemical companies may face increased downtime and the possibility of increasing a company's environmental footprint. If biobased feedstocks are obtained in environmentally controversial ways, they can hinder a company's decarbonization efforts. For example, critics have linked palm oil, which is used to make oleochemicals found in detergents and cosmetics, to deforestation of the tropical rainforest. Others have raised concerns about increased competition for farmland used to produce foodstuffs.
The increased use of environmentally friendly biobased feedstocks, along with efforts to reduce GHG emissions and plastic waste, is crucial to developing a circular economy as consumer demand drives the creation of a greener world. Depending on future regulations and changes in consumer preference, chemical producers may need to find new ways to reduce GHG emissions and plastic waste while using more renewable feedstocks. Fortunately, companies can tailor their sustainability initiatives by selecting from multiple paths to meet their individual circumstances.
How Exponent Can Help
Including industry experts in environmental and polymer science, data sciences, and chemical, electrochemical, mechanical, and civil engineering, Exponent's sustainability team regularly supports the research, development, and assessment of breakthrough technologies. As companies rapidly pivot operations in response to changing climate conditions and stakeholder expectations, our team can help in the transition to sustainable practices by mitigating risk and devising customized solutions.
Insights
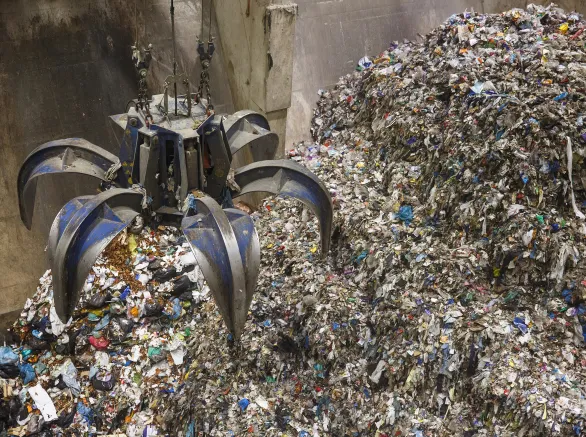