Multidisciplinary expertise for your toughest polymer and composite materials challenges.
Polymers and composite materials are used in a wide range of applications in every industry, and stakeholders at every stage of the product lifecycle benefit from the oversight and consultation of a team of experts who understand the complexities and challenges of polymer sciences and related disciplines.
Exponent supports clients with a breadth of services spanning product liability, intellectual property, failure analysis, quality analysis, product development, recall support, evaluation of materials, life prediction and fitness for service evaluations, and sustainability.
Capabilities
Our Capabilities Are Unparalleled
With expertise in over 90 disciplines and hundreds of capabilities, tools, and methodologies — we get to the root of even the most complex challenges and give you the objective answers you need.
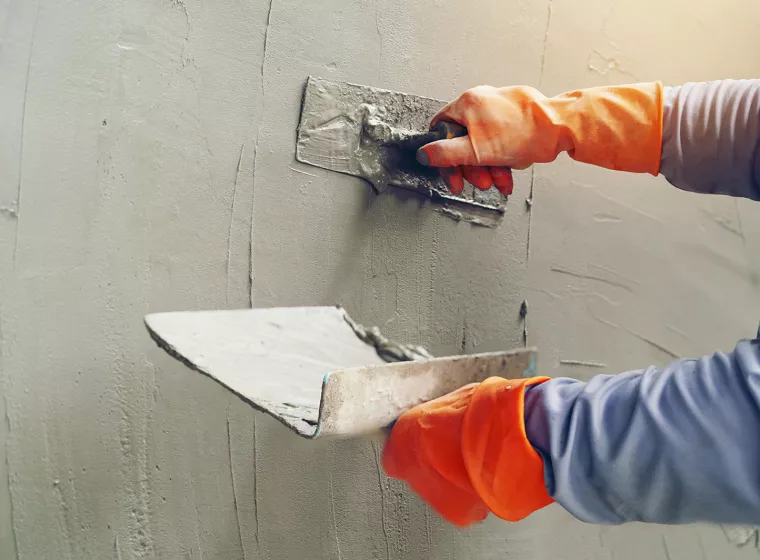
Polymers Used for Construction Materials
Gain insights into the polymers and materials used in all types of construction projects.
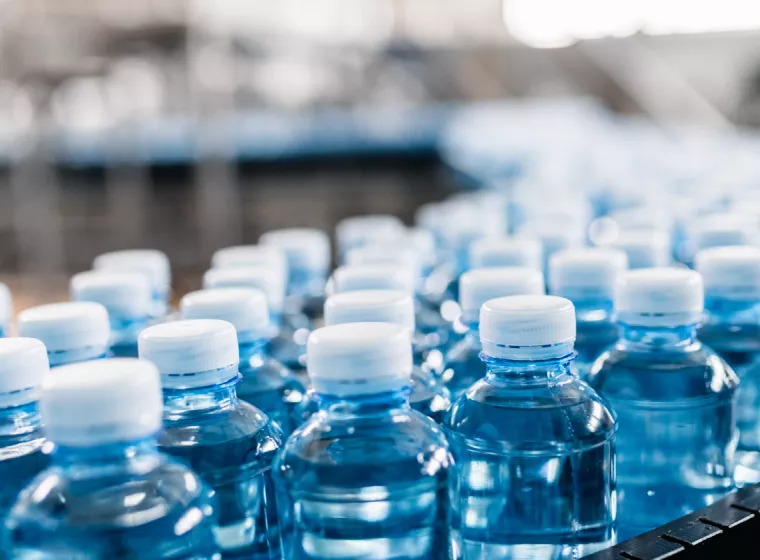
Polymers Used for Food & Beverage Packaging
Create safer, compliant, and high-performing food and beverage products.
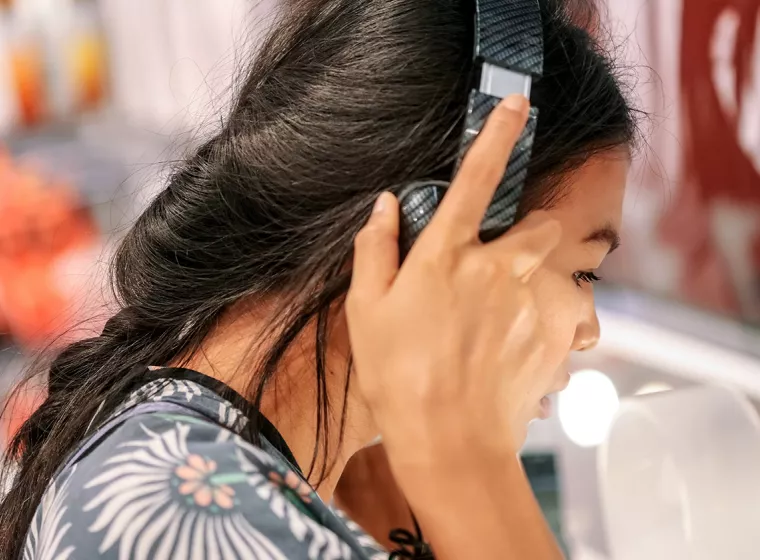
Polymers Expertise for Consumer Products
Rigorous testing and analysis of polymers in consumer products.
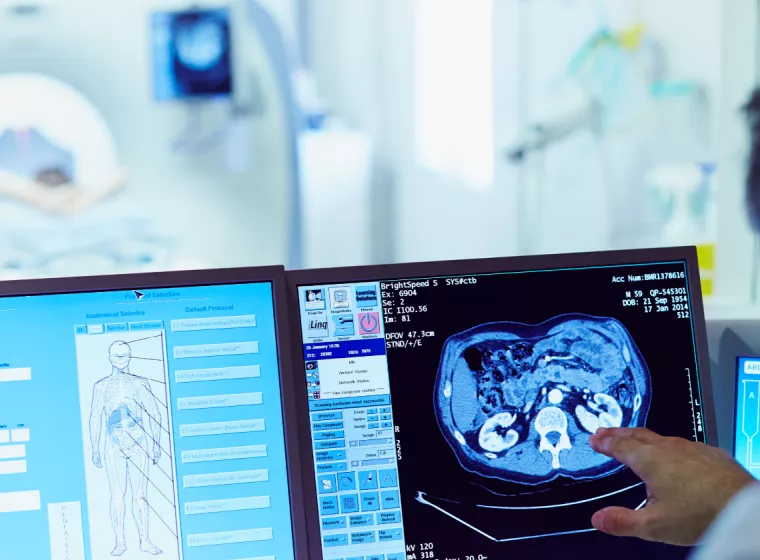
Materials Used in Medical Devices, Implants & Surgical Tools
Expert evaluation of the materials used in medical devices, implants, and surgical tools.
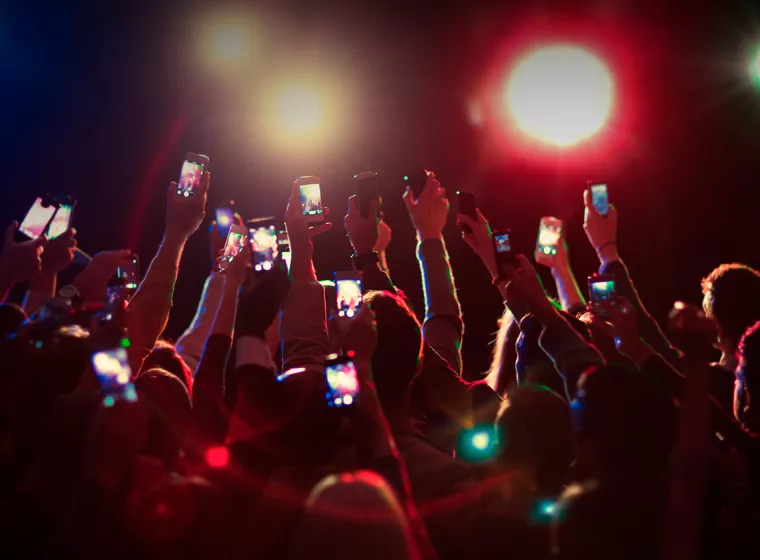
Polymers & Materials Used for Consumer Electronics
Select, optimize, and test polymers and materials used in consumer electronics.
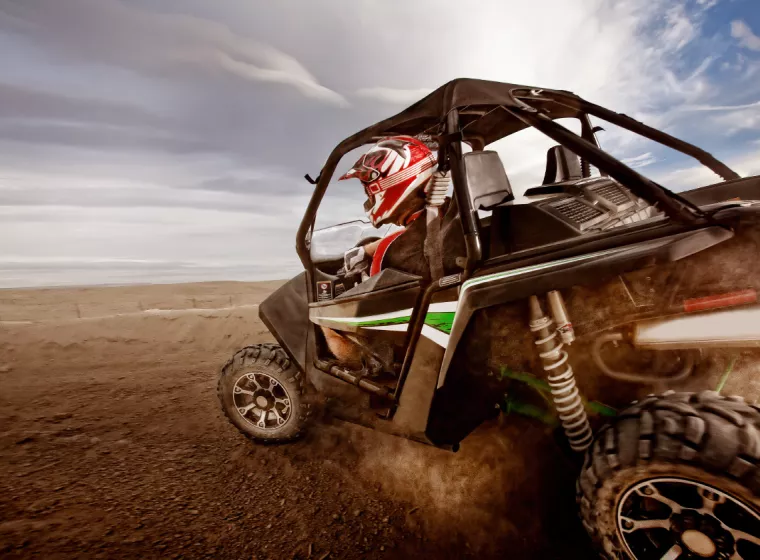
Polymers & Plastics in Automotive & Recreational Vehicles
Evaluate the strength and performance of polymers in automotive and recreational vehicles and marine applications.
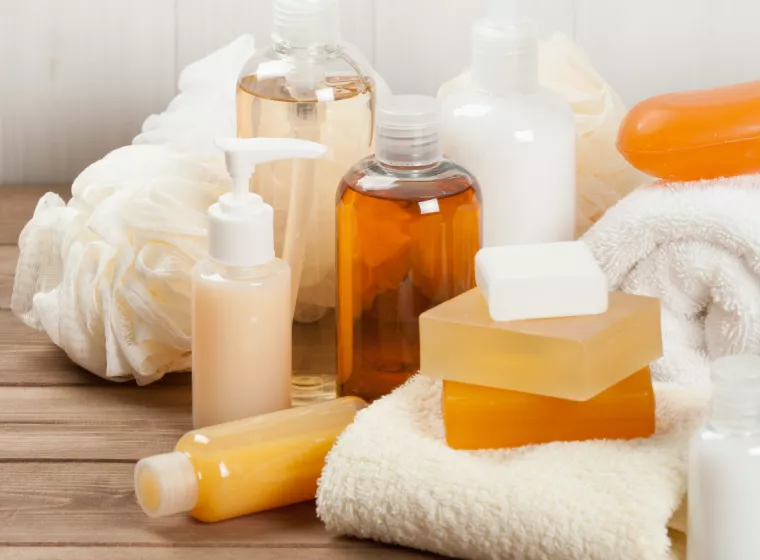
Personal Care Products & Cosmetics
Verify and validate the ingredients in personal care and cosmetic products.
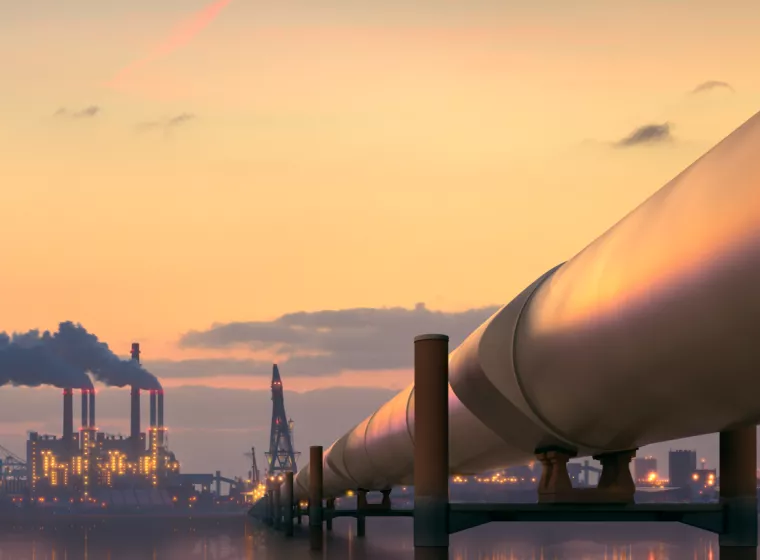
Polymeric Materials Used in the Oil and Gas Industry
Optimize the performance of polymer materials used in oil and gas.

Batteries & Energy Storage
Supercharge performance, reliability, and safety across all stages of the battery and energy storage product lifecycle.
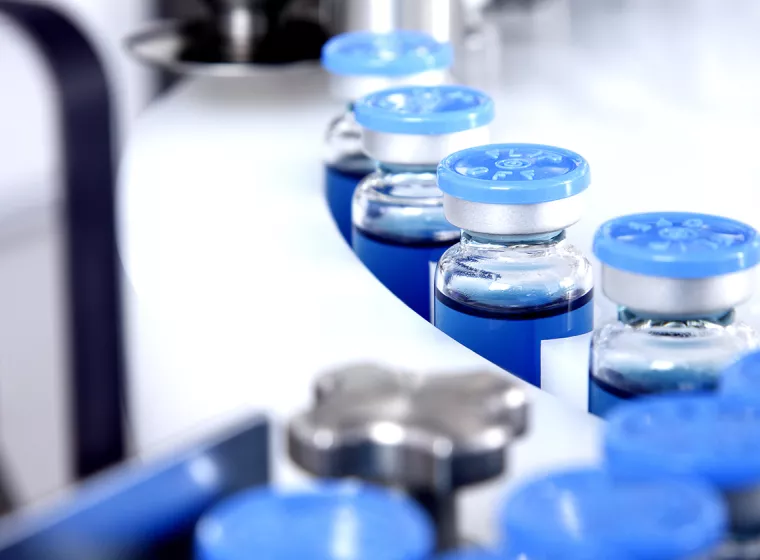
Pharmaceuticals: Chemistry, Manufacturing & Controls
Evaluate next-generation pharmaceuticals with support for research, development, and formulation.
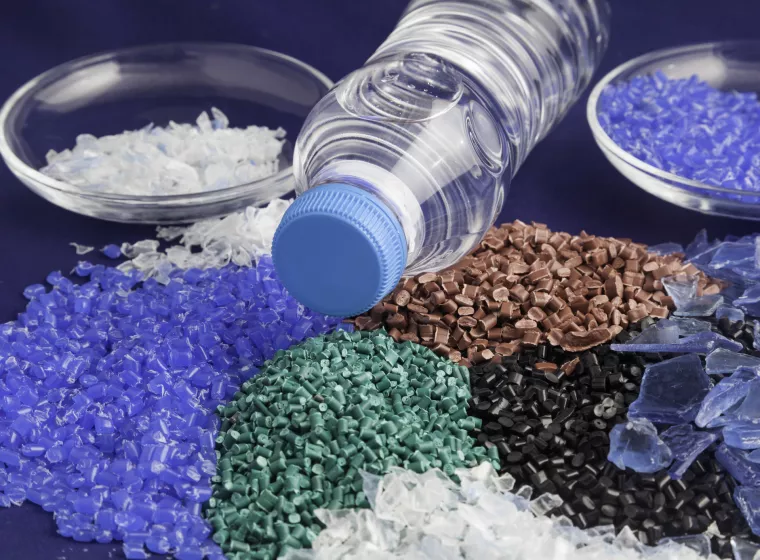
Polymers & Chemistry IP Consulting
Exponent offers expert, bespoke intellectual property consulting services and support for polymers and materials chemistry.
